Guide to Bin Replenishments
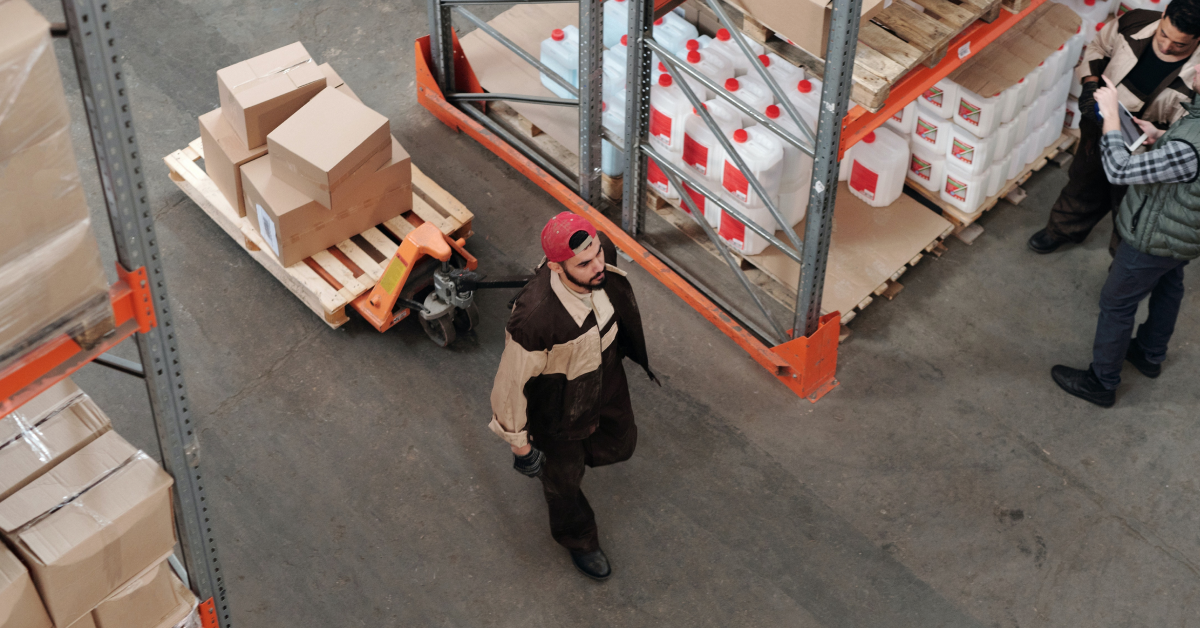
Introduction
For merchants that use Bin Level Inventory, establishing a replenishment plan is essential to making sure that the picking team can continue to get customer shipments out the door as quickly and efficiently as possible.
Using Bin Level Inventory means that you have separate areas in your warehouse for overstock and pickable locations, and bin replenishments are the act of transferring inventory from overstock to pickable.
Without these replenishments, the picking team can quickly become blocked as the inventory in the overstock location is typically not available for assigning to customer shipments.
In last week’s two-part post on optimizing the layout of your warehouse, we covered how to optimize the layout of the bins in your warehouse; this week, we’ll be covering how to use bin replenishments to make sure that this optimized layout is running smoothly.
The goal of an effective bin replenishment plan is to:
- Minimize the handling of inventory - only replenish when needed
- Reduce foot traffic
- Prevent pickers from being blocked from fulfilling orders - make sure they always have inventory available to them in pickable locations
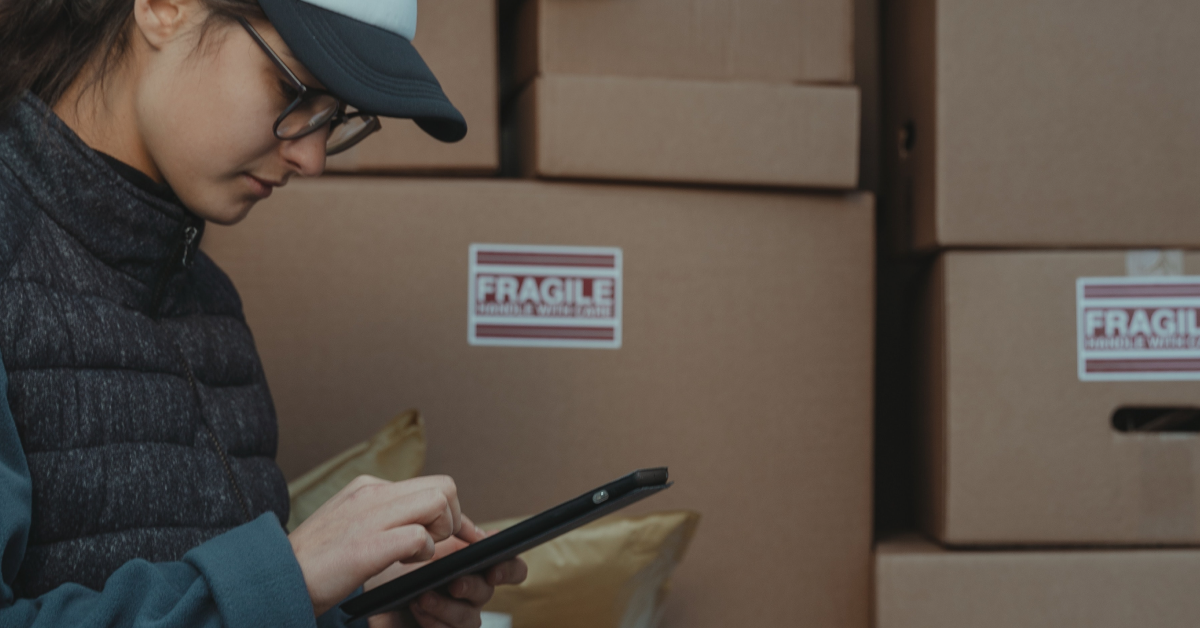
Establishing a Plan
Before determining a plan for bin replenishments, it’s important to ensure that your warehouse layout is optimized based on the sales velocity of your SKUs, which is especially important headed into BFCM.
Once the layout of your warehouse bins is determined, the next step is to establish the minimum and maximum levels of each bin. The minimum is the threshold at which a bin replenishment will be triggered automatically, and the maximum is the level at which the bin will be refilled to.
The maximum is limited by the size of the bin - there is a physical space constraint to each pickable bin, and the amount of product that fits into each bin will determine the max level. The minimum should be determined by three factors:
- Number of expected orders per day
- Expected frequency of replenishments
- Batch size
{{cool-component}}
For faster moving products, the minimum should be higher, to avoid running out of inventory for the picking team. In contrast, slower moving products can have a much lower minimum, as the likelihood of running out of inventory to pick is much lower.
For example, if you’re replenishing once per day, and you have two products, A and B, with:
- A = 10 sales per day
- B = 2 sales per day
Then A should have a minimum of at least 10, while B can have a lower minimum of 2.
Additionally, batch size should be taken into consideration for single unit shipments. For example, if you have a single unit shipment batching template established, for high velocity SKUs, with a minimum batch size quantity of 25, you should make sure that the minimum threshold on the bin is at least 25, to ensure 1 full batch can be picked without interruption.
Executing the Plan
After the plan has been established (with the min/max levels for all bins), bin replenishments will start to be generated and will need to be prioritized. As a general rule, you should prioritize replenishments that contain inventory that are blocking the picking team.
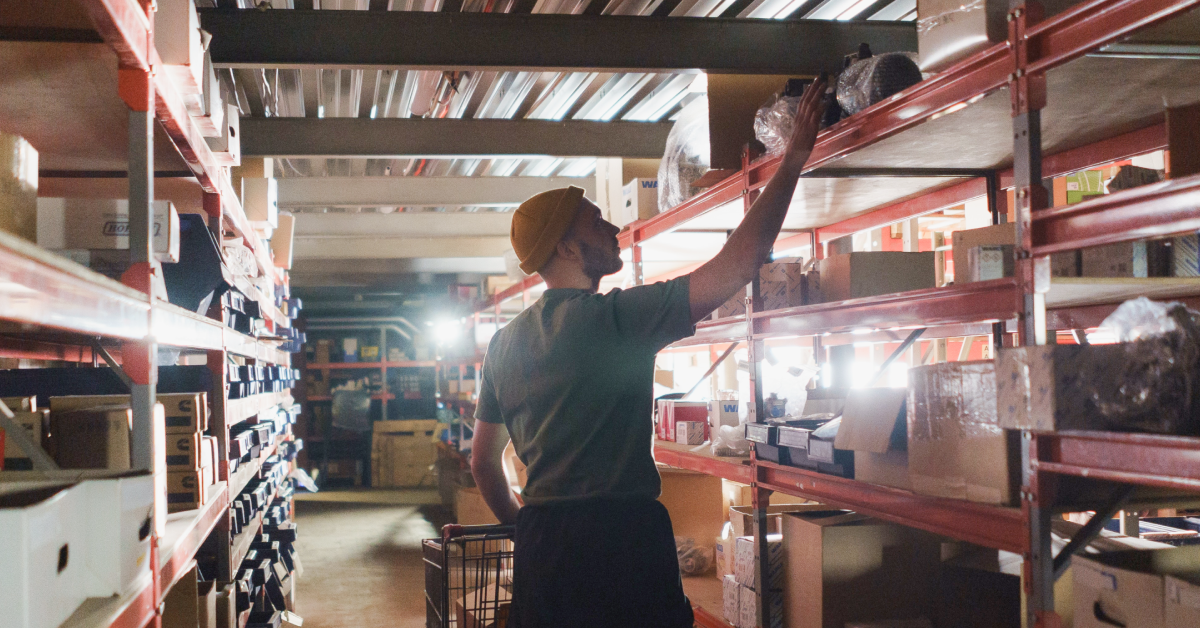
In other words, if there are customer shipments that are waiting for allocation of inventory, as there is none available in pickable locations, complete these bin replenishments first to unblock the picking team. Fulfil makes this easy by:
- Automatically generating bin replenishments based on the min/max levels
- Sorting them in order of priority based on orders that are waiting allocation
Next, it’s important to consider when these bin replenishments should occur. If possible, bin replenishments should occur during shift changes, or before/after a shift starts/ends. This is to reduce foot traffic as much as possible by not having the picking team and the replenishment team in the same place at the same time. If your warehouse team is large enough, you can establish a dedicated replenishment team to manage this workflow. Alternatively, it’s also possible to use the same team to replenish and pick, which can also avoid the foot traffic congestion problem entirely.
Looking Ahead
Finally, any operations plan should be constantly measured and evaluated on an ongoing basis to determine how well it's working. For bin replenishments, you should be monitoring to see if replenishments are:
- Happening often enough - meaning that pickers are not waiting for pickable inventory to be available to them
- Happening too often - resulting in too much foot traffic to the bins and a slower rate of getting shipments out the door
Based on your ongoing analysis, you can adjust accordingly by increasing the frequency of your bin replenishments, adjusting the min/max levels of each bin, or expanding the pickable locations of fast moving SKUs to additional bins.
For more information about how Fulfil makes it simple to keep your warehouse team running smoothly, book a demo with our team!
{{guide-form-component}}
Get Your Free Guide to Ecommerce ERP
More Reads on the Fulfil Blog
.png)
How Hoss Improved Their Amazon Seller Health with Fulfil’s Amazon Integration
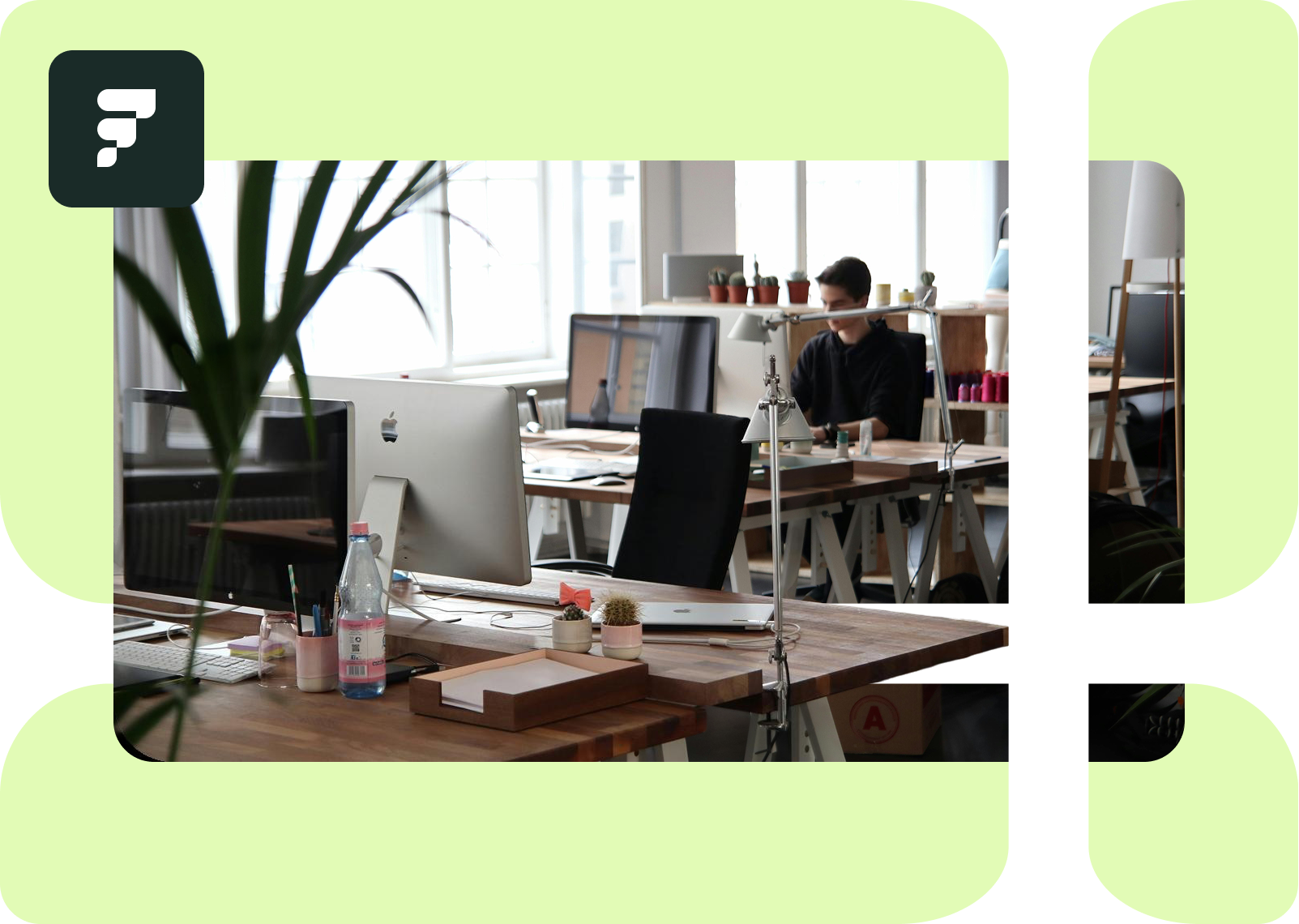
How Your Accounting Software Should Help Overcome Ecommerce Bookkeeping Challenges
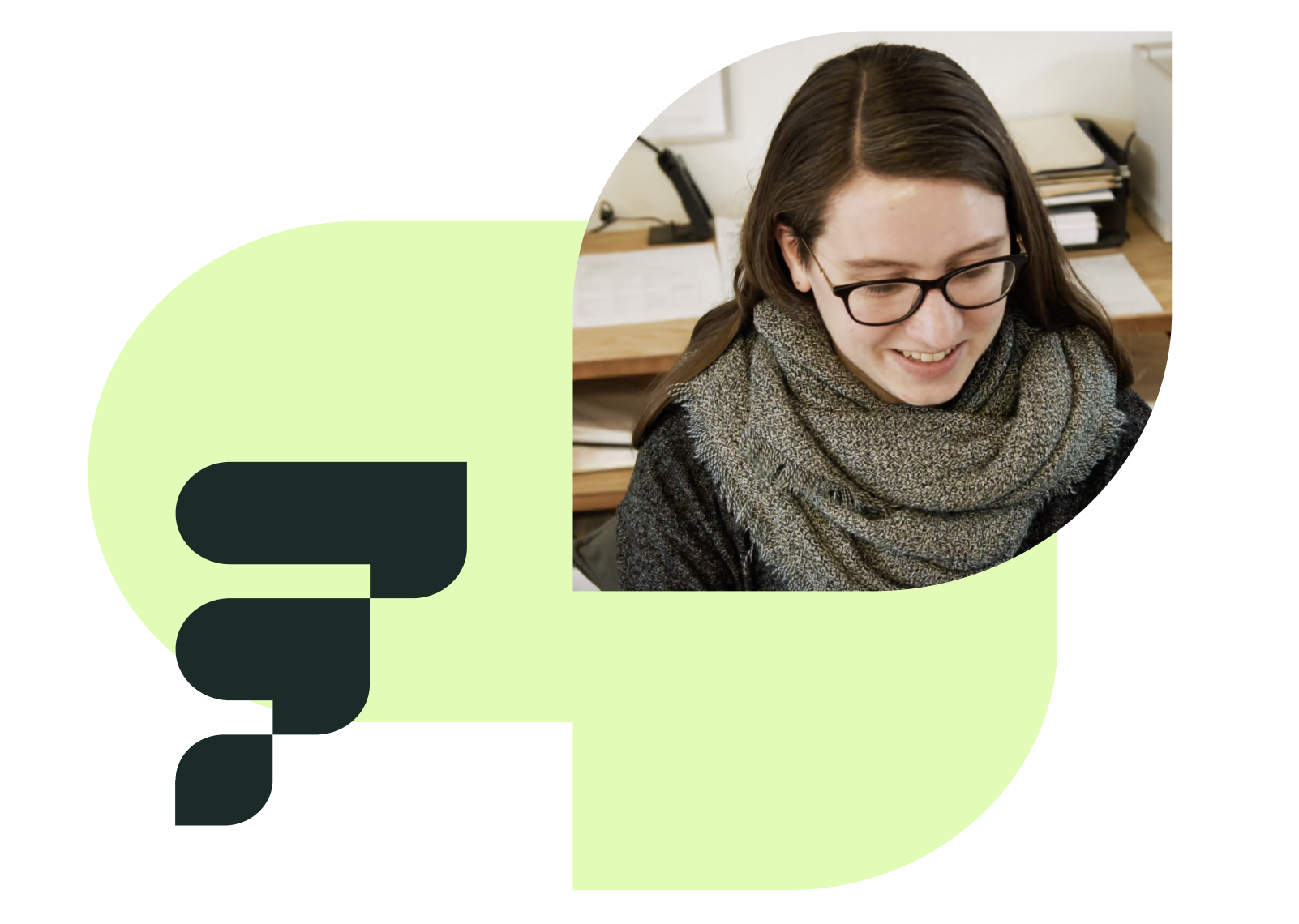
Revenue Recognition: Beyond the Basics
Get started easily with a personalized demo
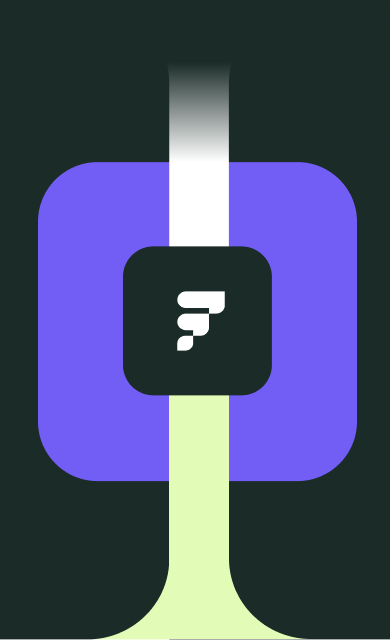