Customer Shipment Batching for BFCM
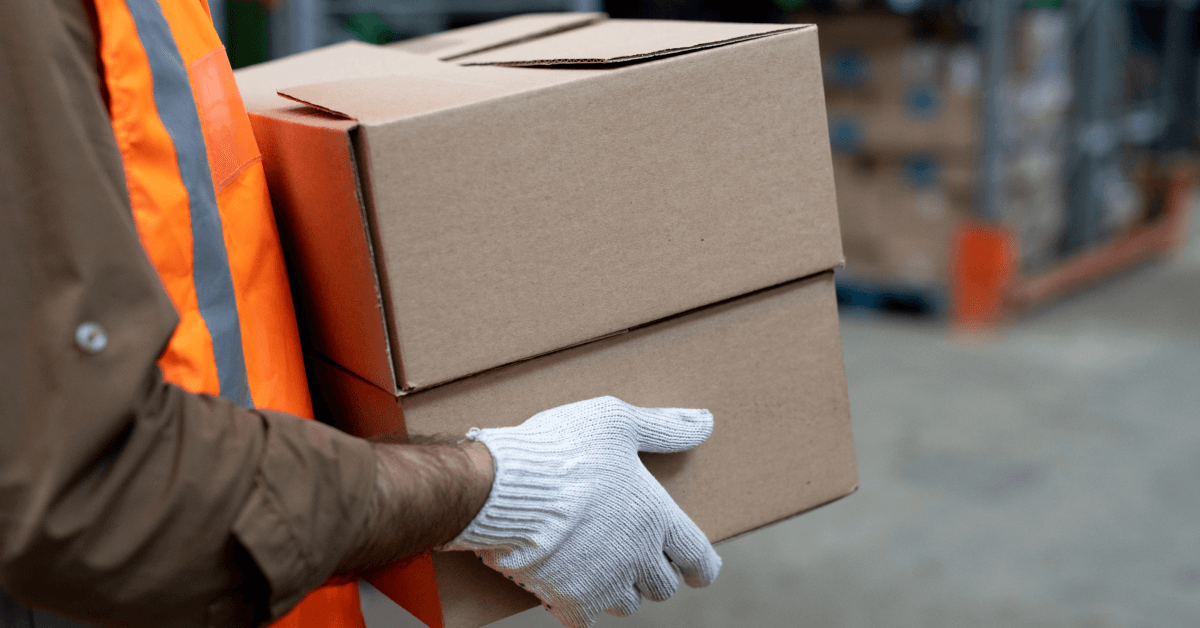
What is Batching?
Batching is the process of grouping a series of Customer Shipments together to make your pick, pack, and ship processes more efficient. These are typically defined by a series of Rules that govern which shipments should be batched together. With Fulfill, you can set up flexible batches based on your needs using our Batching Template wizard.
Why do you need to use Batching?
Picking can quickly become a bottleneck in most warehouses, which can become exacerbated by the increased volume of BFCM. The Picking team, in particular, can benefit greatly from Shipping Batches, as multiple shipments can be picked simultaneously, resulting in faster order fulfillment.
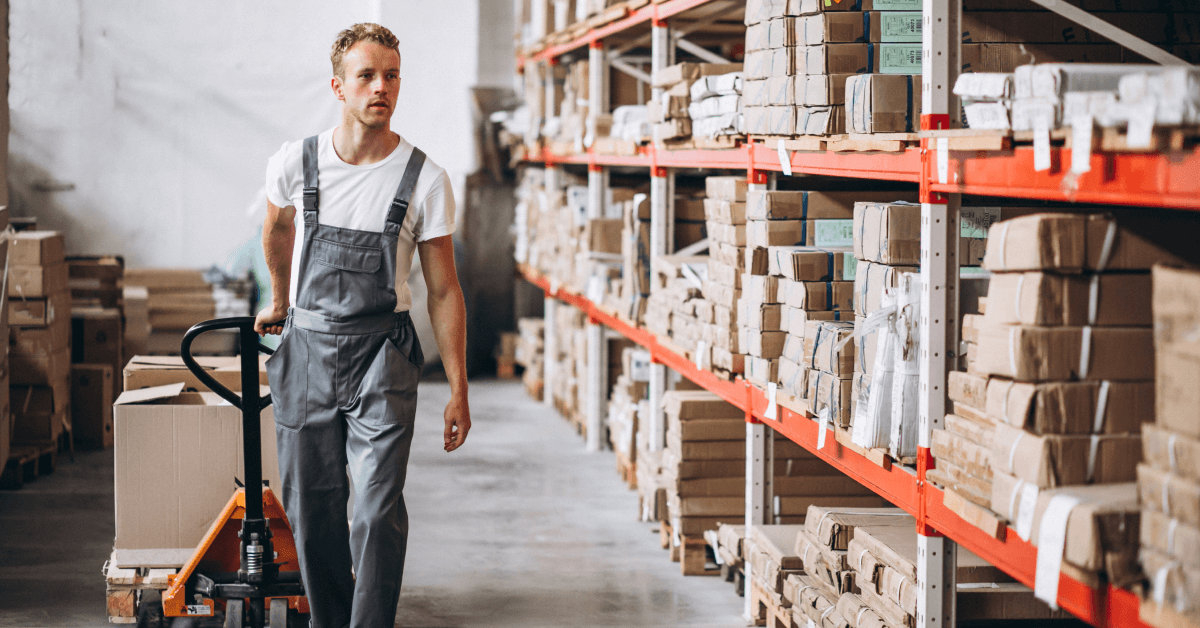
Recommended Batching Logic
The following criteria should be used to group Customer Shipments together:
Batch Template #1 - Single unit shipment (not single line item)
These are any shipments that only contain a single unit. When batched together, a single picker can quickly and efficiently pick a large number of orders as each order is small and simple. These are also great to give to temporary warehouse staff, as typically the packaging, weight, and carrier are all predetermined – reducing the opportunity for human error. With Fulfil, this process is further optimized as Fulfil will automatically split single unit batches on an individual SKU basis, when a single SKU has enough shipments to meet the minimum quantity of the batch. This means that the Picker will be even more efficient, as they will likely only need to go to a single bin.
Batch Template #2 - Single line item shipments
A single line item shipment means that there is only a single product per order, but there may be multiples of this product. Separate them from Single Unit shipments as they may require multiple boxes, weighing, different carriers, and generally have more variation in picking, packing, and shipping workflows.
Batch Template #3 - Multi-line item orders
Continuing the pattern of increasing complexity, these orders contain multiple products, with a possibility of having a quantity greater than 1 for each product. These shipments should be separated out from the easier to pick orders, so that they don’t slow down the simpler orders from getting out the door. You can also use this method to create a batch of shipments containing products from a particular picking zone, minimizing Pickers' walking routes.
Batch Template #4 - Orders with customization/personalization
Finally, any product that requires a level of customization or personalization, such as engraving, should be separated into a separate shipping batch. These products will likely need to be sent to a different area of the warehouse, and should be grouped together to increase the efficiency of these inventory movements. These batches should be handled by more experienced staff, and the simpler batches can be tackled by your newer or temporary warehouse staff.
{{cool-component}}
Using Batching in the Warehouse
Size and Frequency
The size of the batch will vary widely depending on the product line, but as a general rule batches should be generated so that they take approximately 20-30 minutes to pick. The number should be large enough to realize efficiency gains, but small enough to allow continuous improvement, and prevent issues such as partially picked batches being abandoned at the end of a shift.
Whenever possible, batches should be generated continuously by the team lead, and not printed in advance. Reason being, anytime a batch is printed, it becomes static, and the system cannot continuously optimize for batching creation if new orders arrive, suppliers ship more inventory, or customers return items.
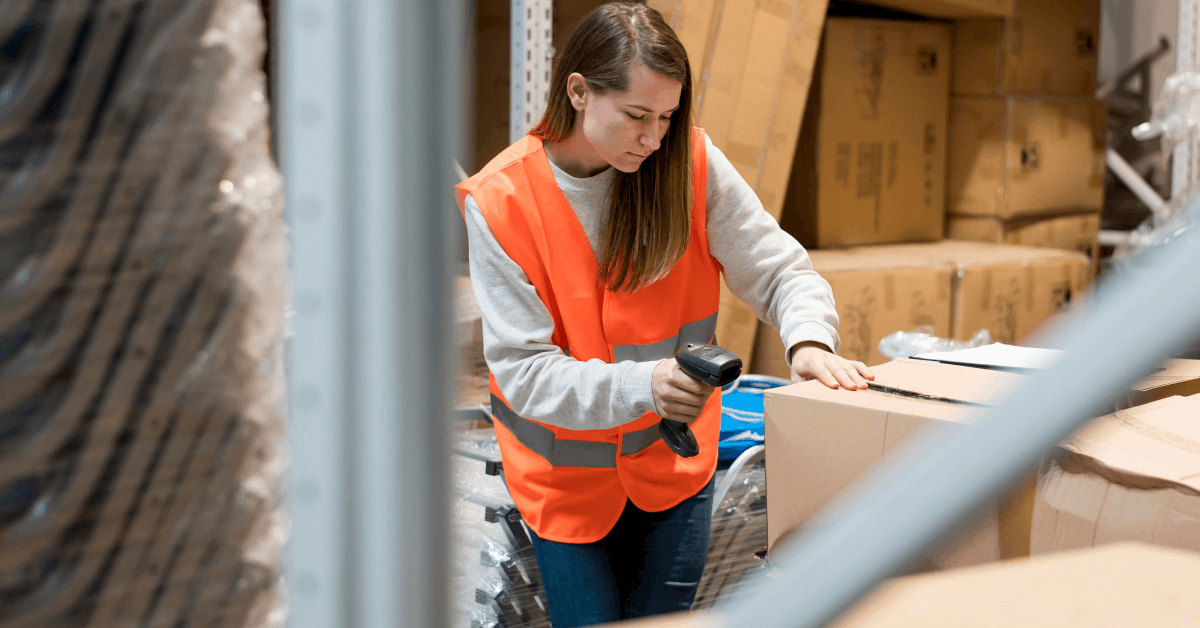
Equipment
The following equipment should be considered when using Batching:
Hand-held scanners
This enables a check and balance at each step of the pick/pack/ship process, and drastically reduces the opportunity for human error.
Carts
These wheeled carts contain a series of Totes, that will make it much easier and more ergonomically friendly for your warehouse team to pick orders.
Totes
These are containers that go in the Carts, which are divided into sections which can each hold an individual order. This makes it easier to keep track of which order is where, and ensure there isn’t a breakdown in communication when handing off to Packing from Picking.
Anti-Patterns
Batching based on Carrier
Merchants will commonly consider the Carrier as a criteria to include when creating Batches. However, the primary focus of Shipping Batches is to increase the efficiency of the Picking team, not the Packing and Shipping team. This is because Picking is often where the bottleneck occurs, far before there would be any level of bottleneck at Packing or Shipping.
Instead, existing Shipment Batches should be Segmented by Carrier. This ensures that the Picking team is able to get the full benefit of the Batching workflow, and the Packing and Shipping team also still have visibility into Carrier information.
Too many Batching Templates (Less is more!)
The Batching engine is only as effective as the rules it's governed by, and with too many Batching Templates competing against each other for the same pool of shipments, the efficiency of each Template will be drastically reduced. This is because even with a high volume of orders, there simply won’t be enough shipments to be able to continuously create efficient batches for the Picking team to use. Our recommendation is to create a maximum of 4 Shipping Batch Templates.
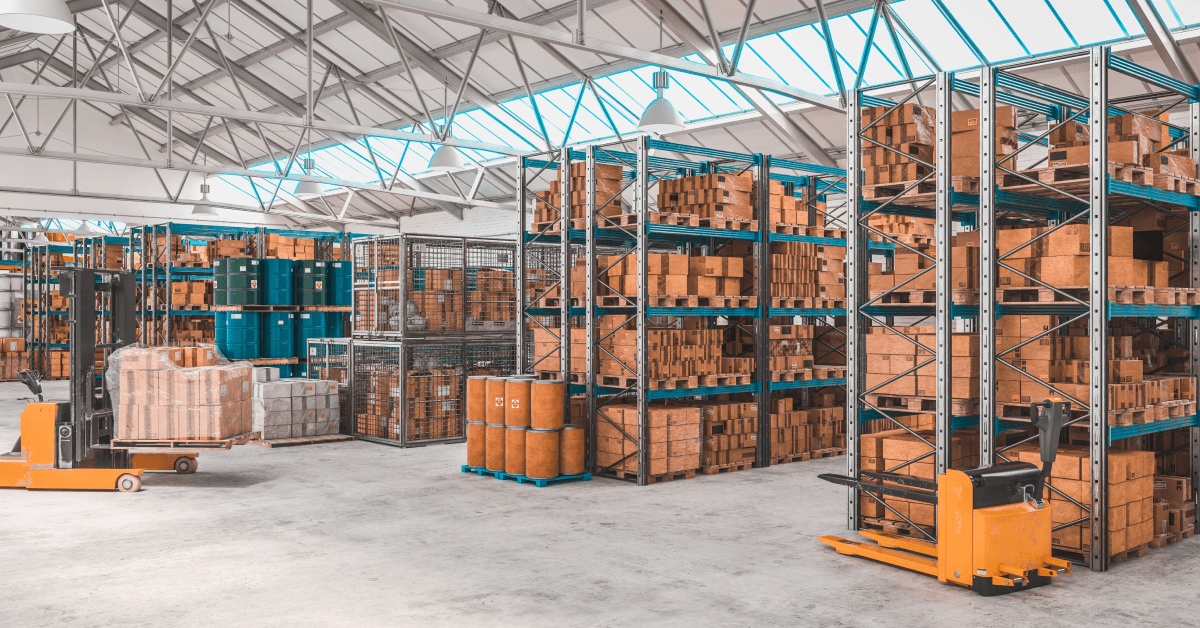
Batching Based on Packing
Batching is primarily meant to optimize the Picking workflow, which is typically the bottleneck in any warehouse operations. Therefore, any Packing requirements shouldn’t be taken into consideration when creating Batching Templates. A common specific example of this is batching based on Packaging Materials, or Box Type.
Summary
Batching Customer Shipments in your warehouse can be an incredibly effective tool to increase the efficiency of your pick/pack/ship team. However, the specific criteria that go into creating the Batching Templates should be carefully considered to ensure that the system can optimize the Batches to provide the largest benefit.
For more information about how Fulfil’s Batching Template Wizard works, and to see how this could help your warehouse team, book a demo to see Fulfil in action!
{{guide-form-component}}
Get Your Free Guide to Ecommerce ERP
Get your free guide to eCommerce ERP
More Reads on the Fulfil Blog
.png)
How Hoss Improved Their Amazon Seller Health with Fulfil’s Amazon Integration
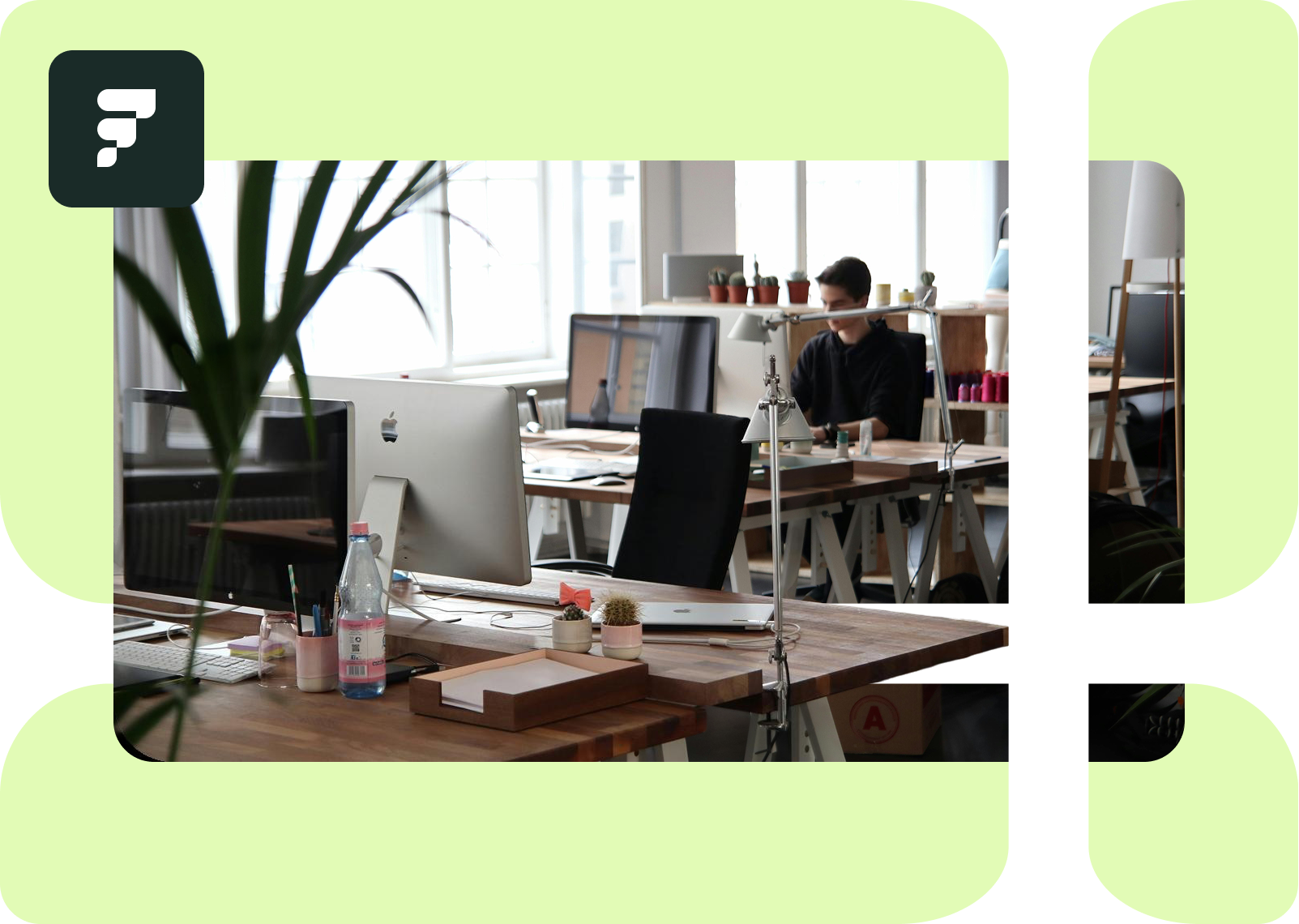
How Your Accounting Software Should Help Overcome Ecommerce Bookkeeping Challenges
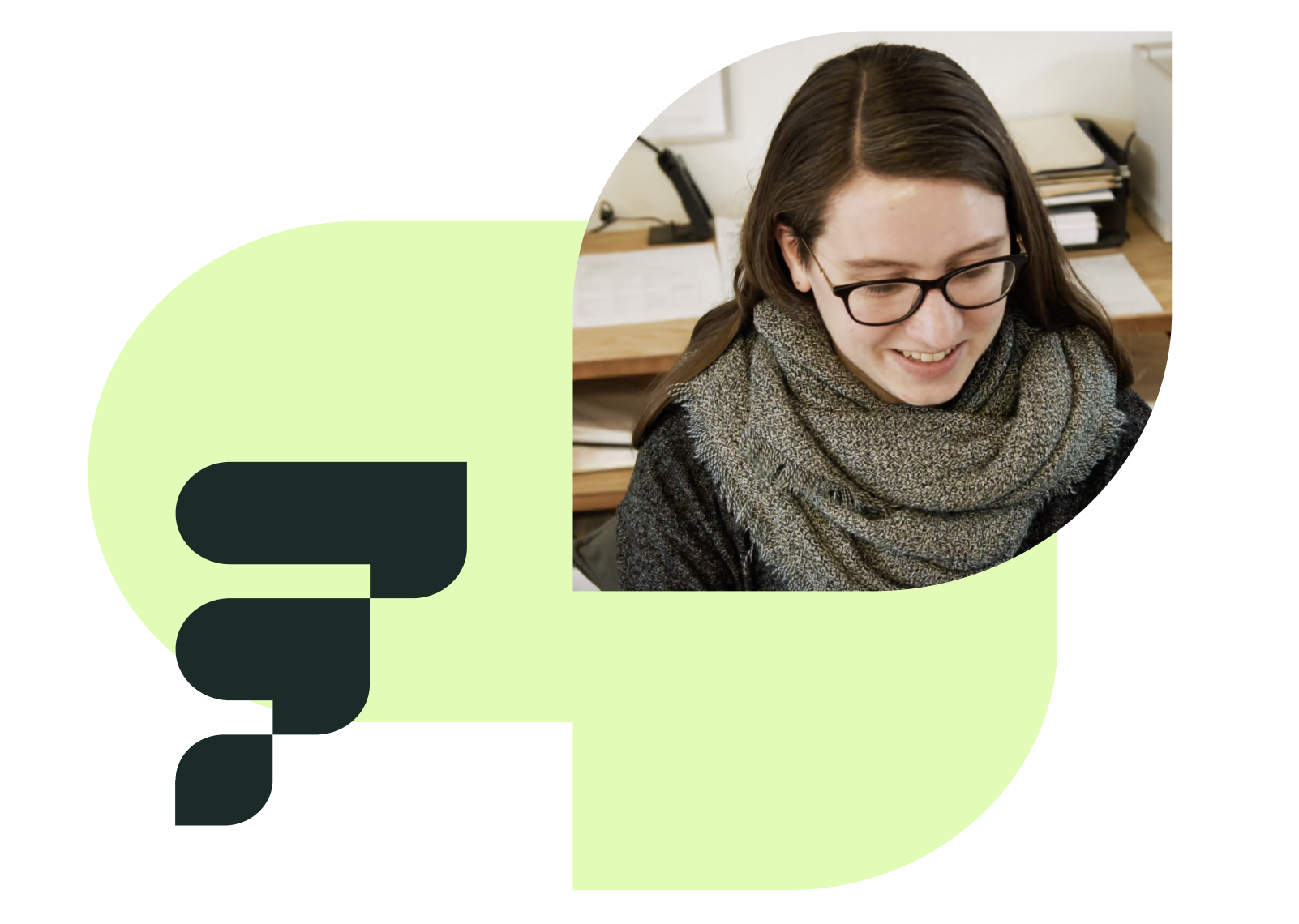
Revenue Recognition: Beyond the Basics
Get started easily with a personalized demo
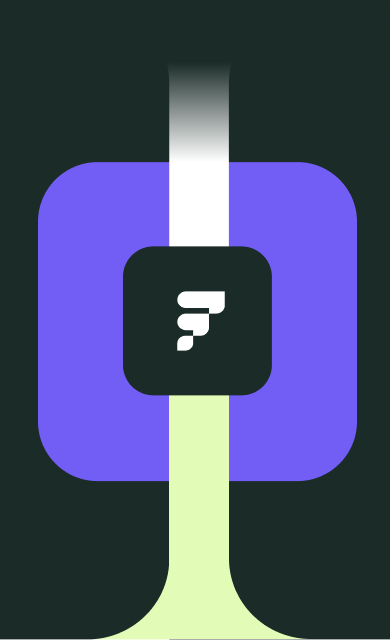