MANUFACTURING
Manufacturing software that grows with your business
Transform your manufacturing operations with software built for modern manufacturers. From simple assembly lines to complex production, Fulfil helps you manage BOMs, track costs, and optimize production workflows—all while maintaining visibility across your entire operation.

TRUSTED BY
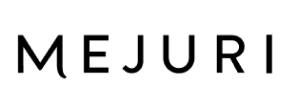
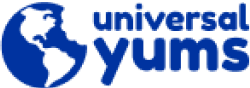
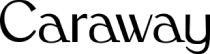
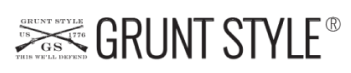
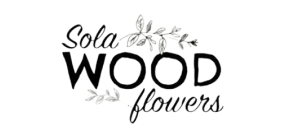

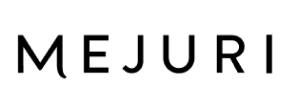
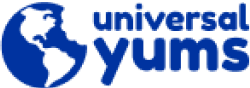
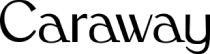
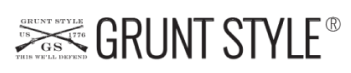
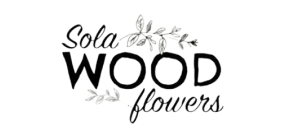

Take control of your manufacturing operations
Automate complex workflows, reduce errors, and fulfill orders faster with intelligent routing and prioritization. Whether you're shipping directly to consumers, dropshipping to marketplaces, or managing large B2B orders, Fulfil adapts to your unique business needs.
Streamline production planning
Run your manufacturing operations exactly how you need—whether you make-to-stock, make-to-order, or both. Automate production requests, manage lead times, and batch similar orders to maximize efficiency without adding complexity.
Optimize shop floor operations
Give your production team the tools they need to succeed with a mobile-friendly interface that tracks progress. Monitor productivity, manage tasks, and handle customization requests—all from a simple, intuitive dashboard.
Track costs with precision
Get complete visibility into your production costs, from raw materials to labor. Calculate weighted average costs, identify inefficiencies, and make data-driven decisions about pricing and profitability.
Core manufacturing features
Take control of your product structure
Build and manage even the most complex product structures with flexible BOM management. Whether you're handling simple assemblies or multi-level production processes, Fulfil adapts to your needs.

Now we have 100% visibility into our raw materials, which is huge, and we’re doing consistent cycle counts to track inventory.

Taylor Moody
CEO, Made by Mary

Flexible BOM management
Create and manage complex product structures with easy component tracking and streamlined production planning.
Work centers and routing
Define production steps, allocate resources efficiently, and optimize workflows to reduce bottlenecks.
Production orders
Create and track manufacturing orders from start to finish.
Make-to-order and make-to-stock support
Flexibly switch between production strategies to optimize inventory levels and meet customer demands.
Nested BOMs
Handle multi-level product structures with clear visibility into all component requirements at every level.
Built-on-the-fly assembly
Support kitting and light assembly operations with custom product configurations.
Repair order management
Handle warranty repairs, manage component replacements, and invoice customers for services seamlessly.
Manage your shop floor processes efficiently
Give your production team control over day-to-day operations with tools designed for maximum efficiency and visibility.

Fulfil has helped us constantly push the ceiling of our production capacity. Once we started using Fulfil, we were able to break our production records. Last year, we did 19,000 pieces in a 12-hour day.

Eve Munguia
Director of Operations,
Lynch Creek Farm
Lynch Creek Farm

Production app
Access a mobile-friendly interface for real-time updates and improved communication between management and operators.
Work orders
Track and manage individual production tasks with detailed documentation.
Flexible task tracking
Add detailed notes to work orders during operations for better process documentation.
Picking and batching
Optimize material collection and order grouping for maximum production efficiency.
Production time tracker
Monitor productivity through a dedicated touchscreen Production UI with step-by-step progress recording.
Shop floor control
Streamline manufacturing time with comprehensive task management tools.
Personalization support
Give floor staff direct access to customization requests on work orders.
Take control of your production expenses
Get complete visibility into your true production costs with comprehensive tracking of labor, materials, and overhead.
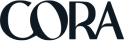
We are super omnichannel. Having a partner like Fulfil that allowed us to handle all our sales channels easily out of the box, without a bunch of custom development being required, was really important for us.

Janaye Pohl
Director of Operations, Cora

Labor costing
Track all labor costs and improve product costing accuracy for better pricing decisions.
Production cost tracking
Monitor production costs in real-time to identify and address inefficiencies quickly.
Automated cost tracking
Maintain accurate cost data for completed and work-in-progress inventory with weighted average calculations.
Connected inventory control
Reserve raw materials before production starts and manage inventory transfers between warehouses efficiently.
Optimize your production schedules
Take control of your production schedule with powerful planning tools that optimize efficiency and reduce waste.
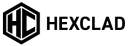
We're going to do 150,000 orders this month. Without Fulfil, there's no way I would be with a smile on my face.

Jason Panzer
CEO, HexClad

Production requests
Automatically generate production orders based on demand to streamline planning and reduce manual intervention.
Production lead time management
Set and manage accurate production lead times to improve delivery date accuracy.
Made-to-order production streamlining
Connect directly to production equipment via API and optimize pre-picking and pre-packing workflows
Production batching
Group similar orders to reduce setup times and optimize resource utilization.
Production planning and forecasting
Make informed decisions about production scheduling in uncertain supply chain conditions.
Meet quality requirements consistently
Maintain high-quality standards and meet compliance requirements while keeping operations efficient.
The increased volume of orders has caused us no issues.

Zach Smith
Director of Operations, RIDGE

Lot number management
Track and manage lot numbers throughout production for complete traceability and simplified recall management.
Outsourced manufacturing
Maintain quality control while managing third-party manufacturing processes and costs.
Integration with inventory and purchasing
Ensure seamless flow of materials with automated procurement based on production needs.
Make informed operational choices with real-time analytics
Get the insights you need to continuously improve your operations with comprehensive reporting and integration capabilities.
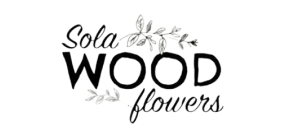
I like Fulfil a lot mainly because their team is very, very, very good. It's the only time I've bought an ERP and did not feel scammed. They were up front about functionality and have been tremendously helpful for us. Highly recommend their team.

Mehtab Bhogal
CEO, Sola Wood Flowers

Production reporting and analytics
Gain insights into efficiency, track KPIs, and identify opportunities for improvement.
Integrated manufacturing workflows
Manage production seamlessly from sales orders through fulfillment.
100% open API
Customize your production process, connect to external tools, and set up automated approval workflows.
CLIENT VOICE
Real results from real customers


Fulfil has helped us constantly push the ceiling of our production capacity higher and higher. We used to produce up to 5,000 units/day. Once we started using Fulfil, we were able to break our production records. Last year, we did 19,000 pieces in a 12-hour day.

Eve Munguia
Director of Operations, Lynch Creek Farm
Everything you need in your ERP
Core manufacturing management
- Bill of Materials (BOM) Management
- Nested BOMs
- Production Orders
- Make-to-Order and Make-to-Stock Support
- Built-on-the-Fly Assembly
- Repair Order Management
- Work Centers and Routing
- Production Orders
Production planning & optimization
- Production Requests
- Production Lead Time Management
- Production Batching
- Production Planning and Forecasting
- Made-to-Order Production Streamlining
Shop floor operations
- Production App
- Work Orders
- Production Time Tracker
- Shop Floor Control
- Flexible Task Tracking
- Personalization Support
- Picking and Batching
Analytics & visibility
- Production Reporting and Analytics
- Integrated Manufacturing Workflows
- 100% Open API
Cost & labor management
- Labor Costing
- Production Cost Tracking
- Automated Cost Tracking
- Connected Inventory Control
Quality & compliance
- Lot Number Management
- Outsourced Manufacturing
- Integration with Inventory and Purchasing
Frequently asked questions
How does Fulfil handle different types of manufacturing processes?
Fulfil supports multiple manufacturing strategies including make-to-stock, make-to-order, and built-on-the-fly assembly. Whether you're doing simple kitting or complex multi-level production with nested BOMs, our system adapts to your processes. You can even manage outsourced manufacturing and repair orders within the same system.
How detailed is the cost tracking?
Fulfil tracks every cost component in real-time – from raw materials and labor to overhead costs. You can monitor WIP inventory values, calculate weighted average costs, and get accurate costing data for completed goods and work in progress. This granular visibility helps you make better decisions about pricing and profitability.
Can Fulfil integrate with our existing systems and equipment?
Yes. Our 100% open API means you can connect Fulfil with any external system – from design software to production equipment. Many customers integrate directly with laser cutters, CNC machines, and other manufacturing equipment. We also integrate seamlessly with inventory and purchasing systems to ensure smooth material flow.
How does Fulfil help with quality control and compliance?
Built-in lot number tracking provides complete traceability throughout the production process. You can easily track components used in each production run, manage quality control checkpoints, and handle any necessary recalls efficiently. For outsourced manufacturing, you maintain the same level of quality control and cost tracking as internal production.
Get started easily with a personalized demo
Our team of experts will assess your needs and goals for a personalized demo tailored for your brand to get you started with confidence.
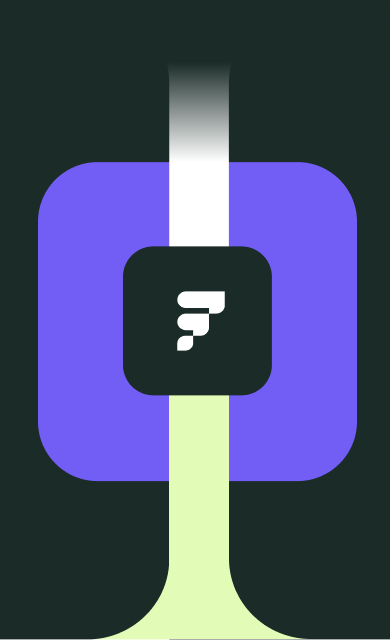
Thank you! Your submission has been received!
Oops! Something went wrong while submitting the form.