Bin Level Inventory 101
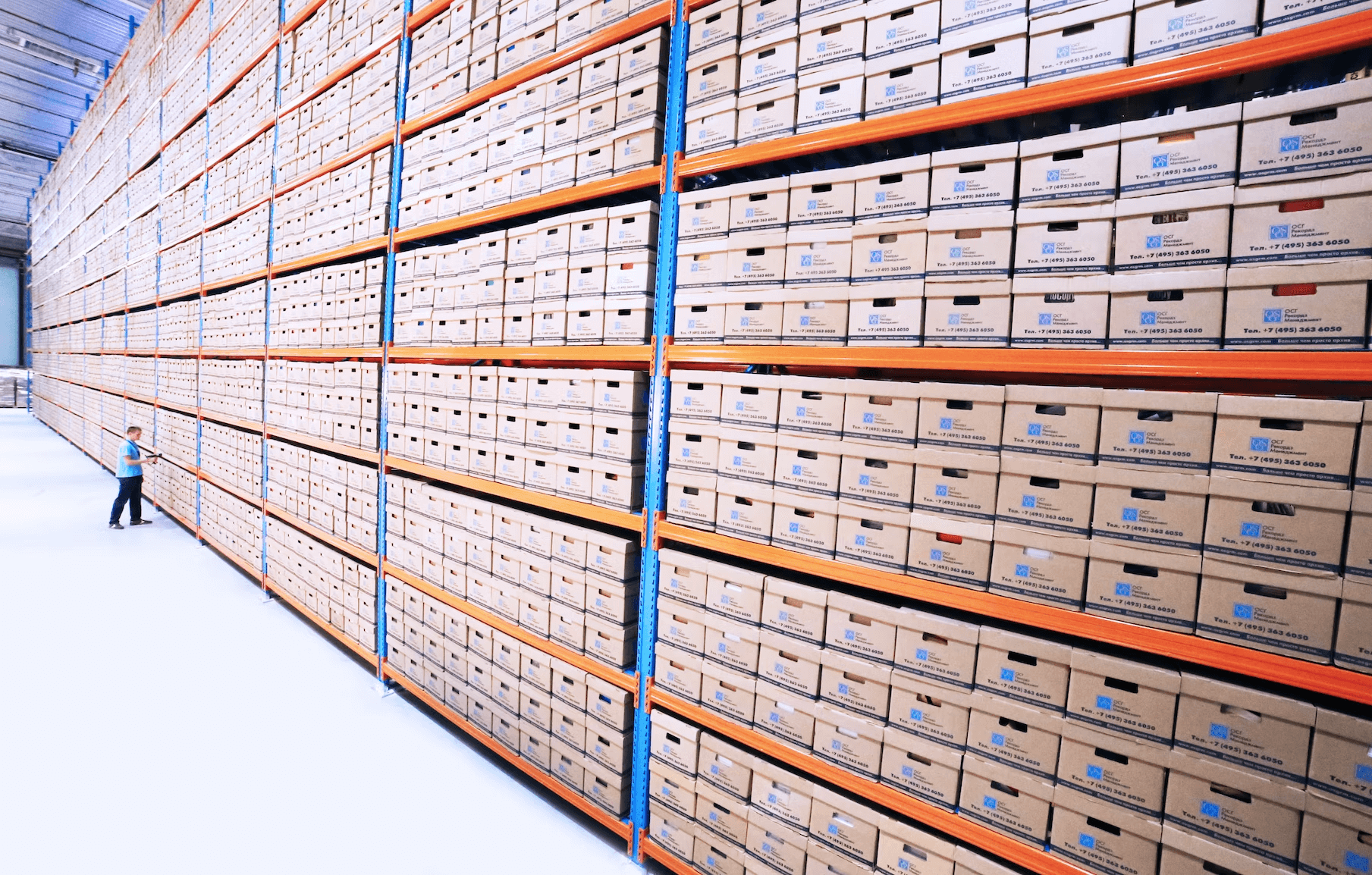
In the same way that having street names and house numbers makes it easier for the postal service and visitors to find your address, having standardized location numbers in the warehouse ensure that your team can:
- Efficiently identify where items are in a warehouse
- Quickly identify which Aisle or section or bin someone is referring to
- Estimate the distance to a specific warehouse location
Typically, when a warehouse is first opened, especially at a smaller scale, inventory is tracked at a Zone level, with inventory received and put away to a general area, rather than a specific rack or bin within the warehouse. While this is absolutely the right choice for smaller warehouse operations, scaling brands often need a finer level of inventory control as the size of the warehouse increases, as well as the number of products.
This inventory visibility can unlock a new standard of control within your warehouse, but also comes at the cost of increased operational overhead. With Zone Based Inventory, it’s possible to get away with looser inventory control - but with Bin Level Inventory, every single inventory movement must be tracked, recorded, and reflected in your software.
Throughout this article you’ll learn about when it makes sense to consider bin level inventory, how to implement, and what it means for your warehouse and operations team.
Definitions
A LOCATION is any area where inventory is stored within your warehouse. This could be anything from a general zone or area, all the way down to an individual bin on a specific rack and aisle.
ZONE BASED INVENTORY is when products are stored in general ‘areas’, rather than tracking specific racks and bins. Typically this also means multiple SKUs are stored together in the same area.
BIN LEVEL INVENTORY is when each individual aisle, rack, shelf, and bin is tracked independently. Typically only a single SKU is stored in each bin. This is usually used in combination with sub-locations for receiving and overstock.
{{cool-component}}
Prerequisites
Here’s how to know you’re ready for Bin Level Inventory:
- Is your warehouse at least 10,000 sq ft?
- Do you have more than 1,000 SKUs?
- Do you release new SKUs at a high velocity (e.g. every week)?
- Do you store the same product in multiple locations within your warehouse?
If you answered yes to at least 2-3 of the above questions, it’s likely time to consider a transition to Bin Level Inventory. If you didn’t, the increased operational overhead likely outweighs any potential benefits that you may see from the revised warehouse structure. That said, this is a transition that almost every eCommerce brand will face at some point - therefore, it’s important to understand the process involved so that when the time comes you can make an informed decision.
Recommended Naming Convention
It’s not uncommon to see newly transitioned warehouses use a letter-dominant naming convention for their individual bins. However, while at first glance this may seem like a reasonable methodology, it actually has the potential to cause significant confusion to the pickers as they navigate the warehouse.
To illustrate this point, consider the following two questions:
- Is the letter S before or after the letter U?
- Is the number 4 higher or lower than the number 7?
Which of these 2 questions was easier to answer? For most, it’s far easier to identify that 4 is lower than 7, versus S is before the letter U.
It is a unique aspect of human psychology that despite both letters and numbers arguably being used a comparable amount, it’s far easier to rank numbers vs letters at a glance. Therefore, the recommended best practice is to use letters for aisles only, and numbers for basically everything else. This will ensure that all bins are human readable, and also help intuitively guide pickers to their destination as fast as possible.
Finally, it’s important to ensure that each bin has a completely unique name or ID associated with it. This will enable the barcoding of locations, and the usage of scanners for the warehouse team to operate efficiently.
Transition Plan
Once the decision has been made to transition to bin level inventory, and the necessary digital setup of the bins has been completed, the physical transition now needs to occur. To start, it always makes sense to complete a cycle count - this results in having the most accurate possible starting numbers for the new warehouse architecture.
Next, it makes sense to carefully consider which items should be placed in each bin. For example, the fastest sellers should be in the bins closest to the starting point of the picking path, with slower movers further away. If you’re using Fulfil, there’s a built-in analytics engine that uses historical sales velocity to intelligently suggest which products to put where, and then intelligently route pickers on the shortest path for each order.
From there, Bin Transfers can be used to transfer the inventory out of the legacy Zones, and into the new individual bins. If possible, do this when you have downtime and there are little or no inventory movements - e.g. evenings or weekends. If that’s not possible, generally aiming for an off-peak period is helpful so that other employees aren’t trying to pick orders at the same time that the transition is happening.
Ongoing Usage
There are 2 critical things to consider when maintaining a bin level inventory setup on an ongoing basis:
- Data Integrity
- Replenishments
Data Integrity
To start - the system that you use is only as good as the quality of information that it's fed. As the old saying goes, garbage in, garbage out, and this absolutely holds true for Bin Level Inventory. Every individual stock movement that happens in the physical warehouse, needs to be replicated in the digital system of record, so that it stays as the Single Source of Truth for your operations. To ensure data accuracy and streamline your processes, consider adopting robust inventory reconciliation strategies to minimize discrepancies and improve overall efficiency.
Otherwise, if someone happens to grab even a single unit out of a bin for a sample, or an influencer order, and doesn’t record this movement digitally, there’s a good chance that a picker will be sent to that bin at some point to pick an order and be met with an empty bin. That said, this can be automated with the usage of barcodes and scanners, which will automatically record the appropriate inventory movements.
Replenishments
Secondly, replenishments are the other key ingredient in the recipe for Bin Level Inventory success. Replenishments can be defined as the process from which the individual bins are refilled from the bulk overstock location. It’s standard practice for merchants to receive purchase orders and supplier shipments in either a pallet, or even a container, and store this excess inventory in the overstock location. From there, a smaller quantity or fraction of a pallet can be stored in an individual bin for pickers to collect orders from.
Calculating the frequency of replenishment is critical to avoiding running out of pickable locations for the warehouse team to collect shipments from. With Fulfil, the Replenishment process can be fully automated, with Bin Transfers being generated based on min and max levels set on each individual bin.
{{guide-form-component}}
Summary
Transitioning to a Bin Level Inventory warehouse architecture can unlock previously unattainable levels of inventory insight, and allow you to have an incredibly fine level of control and visibility into your warehouse operations. That said, it’s important to consider whether it makes sense for your particular situation, and also whether the necessary controls and processes are in place in order to be able to successfully maintain.
If you’re interested in learning more about Bin Level Inventory, and how you can use Fulfil to manage your warehouse, get in touch with our team for more information.
Get Your Free Guide to Ecommerce ERP
Get your free guide to eCommerce ERP
More Reads on the Fulfil Blog
.png)
How Hoss Improved Their Amazon Seller Health with Fulfil’s Amazon Integration
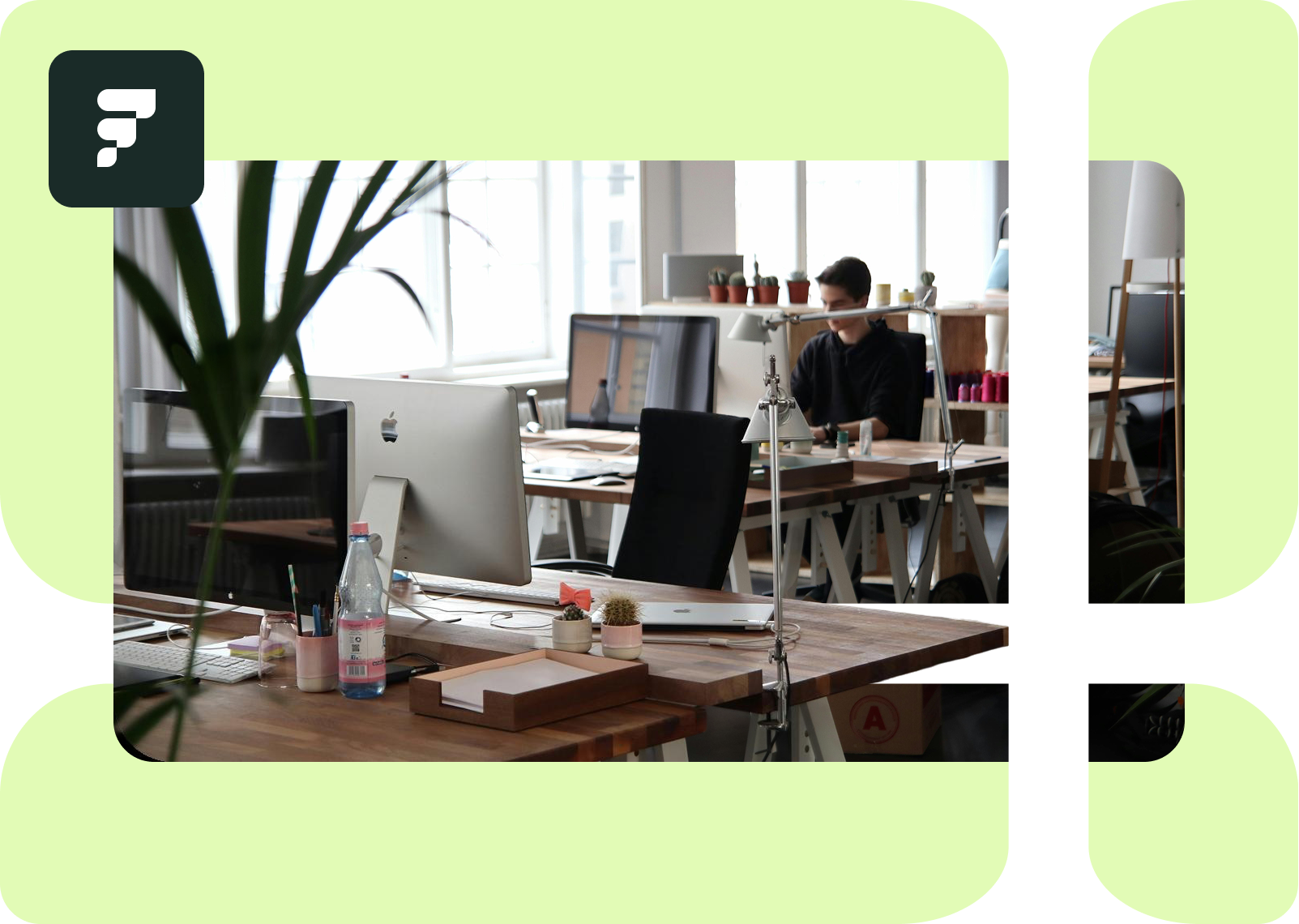
How Your Accounting Software Should Help Overcome Ecommerce Bookkeeping Challenges
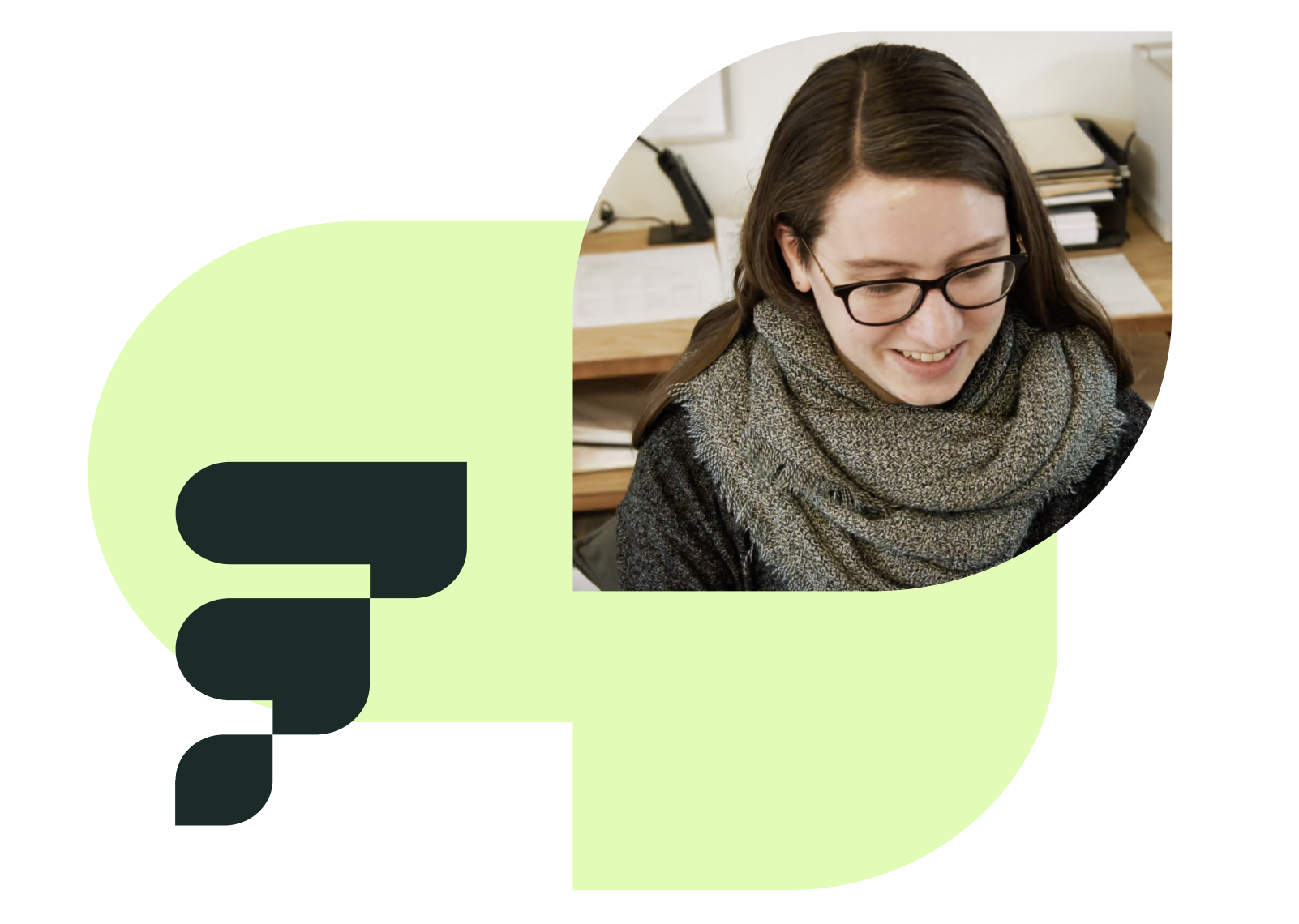
Revenue Recognition: Beyond the Basics
Get started easily with a personalized demo
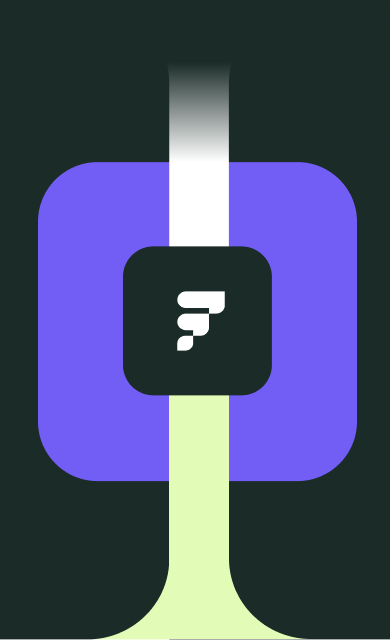