WAREHOUSE MANAGEMENT
Optimize your warehouse operations across all channels
Streamline picking, packing, and shipping with Fulfil's powerful warehouse management system. Eliminate inefficiencies and get real-time visibility and control over your entire fulfillment process
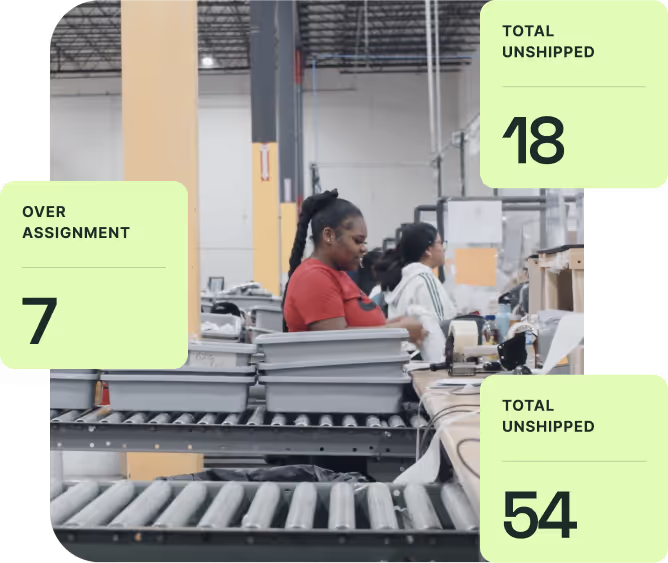
TRUSTED BY
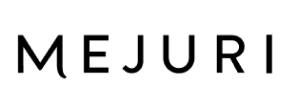
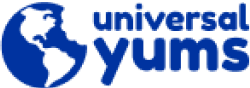
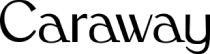
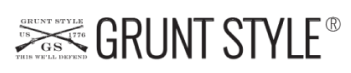
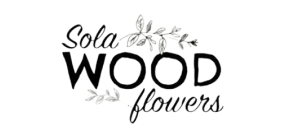

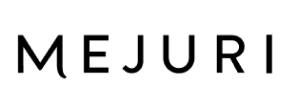
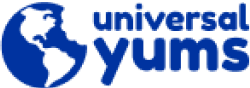
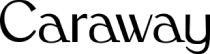
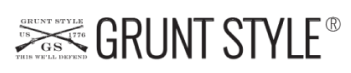
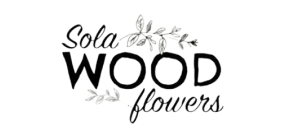

eCommerce-optimized warehouse operations
Automate complex workflows, reduce errors, and fulfill orders faster with intelligent routing and prioritization. Whether you're shipping directly to consumers, dropshipping to marketplaces, or managing large B2B orders, Fulfil adapts to your unique business needs.
Mobile-friendly picking and packing
Empower your warehouse staff with our intuitive mobile app. Optimize pick paths, scan barcodes for accuracy, and manage tasks in real-time, boosting productivity and reducing errors.
Seamless multi-channel inventory management
Eliminate stockouts and overselling with Fulfil's real-time inventory tracking across all sales channels. Our unified platform provides a single source of truth, enabling you to manage stock levels effortlessly and scale your business with confidence.
Flexible fulfillment options
From cross-docking to kitting and bundling, Fulfil seamlessly integrates diverse fulfillment strategies into your workflow. Easily manage special requests, partial shipments, and value-added services without disrupting your operations.
Strong features for efficient operations
WAREHOUSE INVENTORY ACCURACY
Maintain precise stock levels across all locations
Sync real-time inventory across warehouses and sales channels to eliminate overselling, minimize cancellations, and boost customer satisfaction.

Now we have 100% visibility into our raw materials, which is huge and we’re doing consistent cycle counts to track inventory.

Taylor Moody
CEO, Made by Mary

Comprehensive inventory visibility and control
Gain instant visibility into stock levels across all locations, reducing overselling and stockouts. Easily manage inventory across multiple warehouses or stores from a single platform.
Precision location and lot tracking
Improve warehouse efficiency and accuracy with detailed bin-level tracking and lot management, ensuring precise stock control and traceability.
Flexible cycle counting
Maintain inventory accuracy without disrupting operations through configurable cycle count schedules, including the ability to create counts on-the-fly for immediate stock verification.
Advanced inventory tracking technologies
Streamline receiving and counting processes with RFID-enabled tools and integrated barcode scanning, dramatically improving speed and accuracy in inventory management.
CENTRALIZED ORDER MANAGEMENT
Data-driven decision-making at your fingertips
Whether you're optimizing pick paths, evaluating staff performance, or fine-tuning your inventory allocation, Fulfil equips you with the analytical tools to make data-driven decisions. Leverage real-time insights to boost efficiency and drive profitability across your entire warehouse operation.
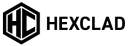
We implemented Fulfil at a key time in 2023. And Q4 was a monster for us. We wouldn't have done it nearly as well without Fulfil.

Jason Panzer
CEO, HexClad

Intelligent warehouse insights and optimization
Make data-driven decisions with customizable reports on warehouse performance metrics. Leverage advanced cartonization algorithms and packing functions to optimize space utilization and reduce shipping costs.
Advanced shipping automation
Set up customizable cut-off times for label generation, automating the shipping process to meet carrier deadlines and optimize delivery timeframes. Streamline end-of-day processes with intelligent shipping rules and automated manifesting.
Real-time visibility and task management
Provide customers and support teams with up-to-the-minute order status throughout the pick-pack-ship process. Assign and track warehouse tasks to improve productivity and accountability, ensuring seamless operations.
STREAMLINED PICK-PACK-SHIP
Accelerate your fulfillment process
Optimize your warehouse operations, reduce errors, and improve order accuracy with Fulfil's advanced picking and packing tools. We handle the complexities, freeing you to focus on scaling your business.
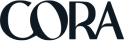
Having a partner like Fulfil that allowed us to handle all our sales channels easily out of the box, without a bunch of custom development being required, was really important for us.

Janaye Pohl
Director of Operations, Cora
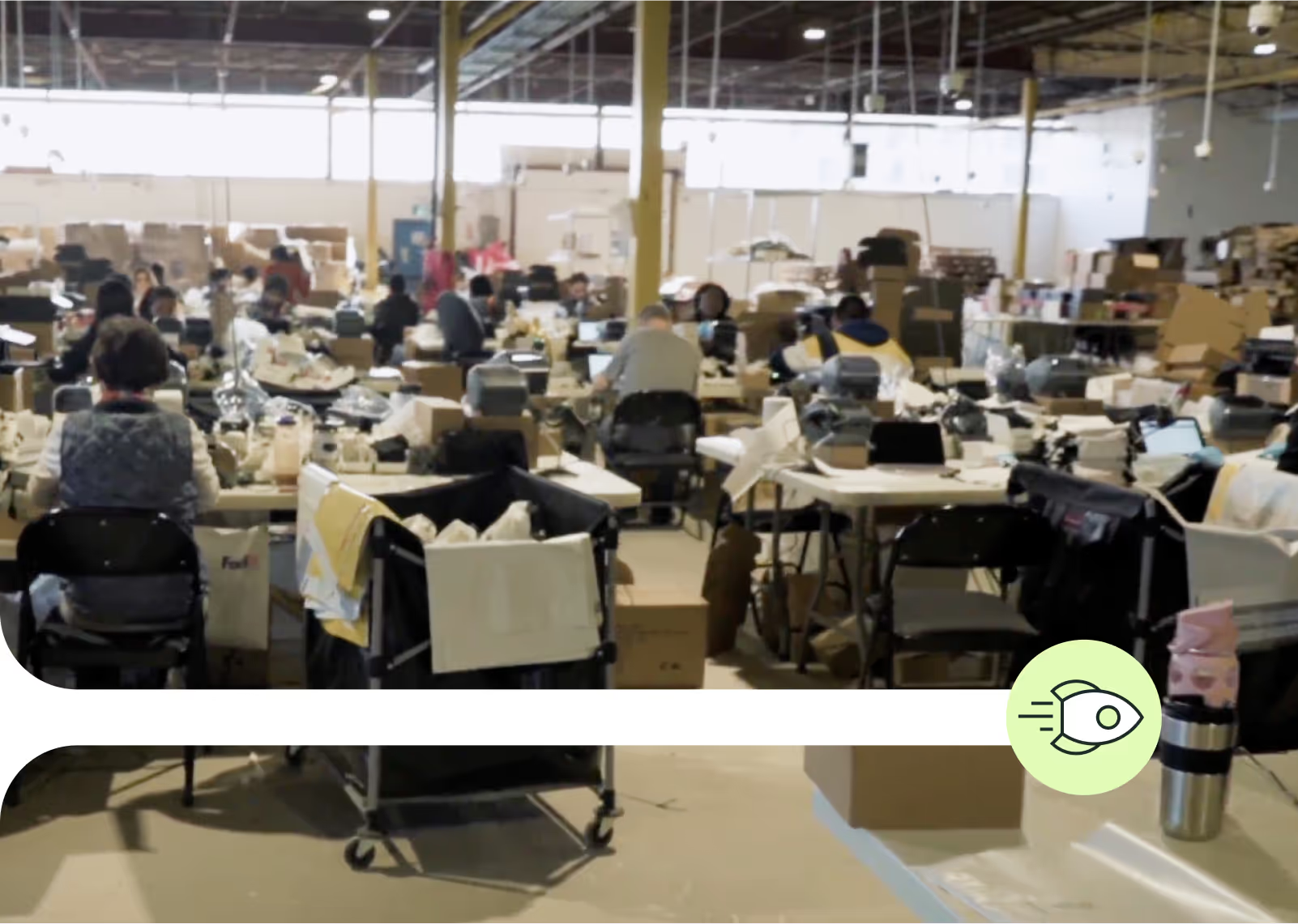
Advanced picking strategies
Boost productivity with flexible picking methods, including batch picking for high-volume operations and zone picking to optimize warehouse layouts and reduce travel time. Leverage single-item batch packing for efficient handling of popular products.
Efficient packing station management
Optimize the packing process with dedicated packing station interfaces, allowing for seamless coordination between picking and shipping operations. Manage multiple packing stations to handle various order types and volumes efficiently.
Streamlined scanning and verification
Ensure accuracy throughout the pick-pack-ship process with easy-to-use barcode scanning and innovative action barcodes that trigger specific system actions, minimizing manual data entry.
EFFICIENT SHIPPING AND RETURNS
Streamline shipping and returns management
Balance customer satisfaction and operational efficiency with Fulfil's advanced shipping and returns features. Turn your fulfillment process into a strategic advantage for your business.
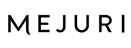
The nice thing with Fulfil is the scale of it. It can bring on a large number of people, get them trained, and get them up to speed in a short amount of time.

Greg Perry
Director of Operations, Mejuri
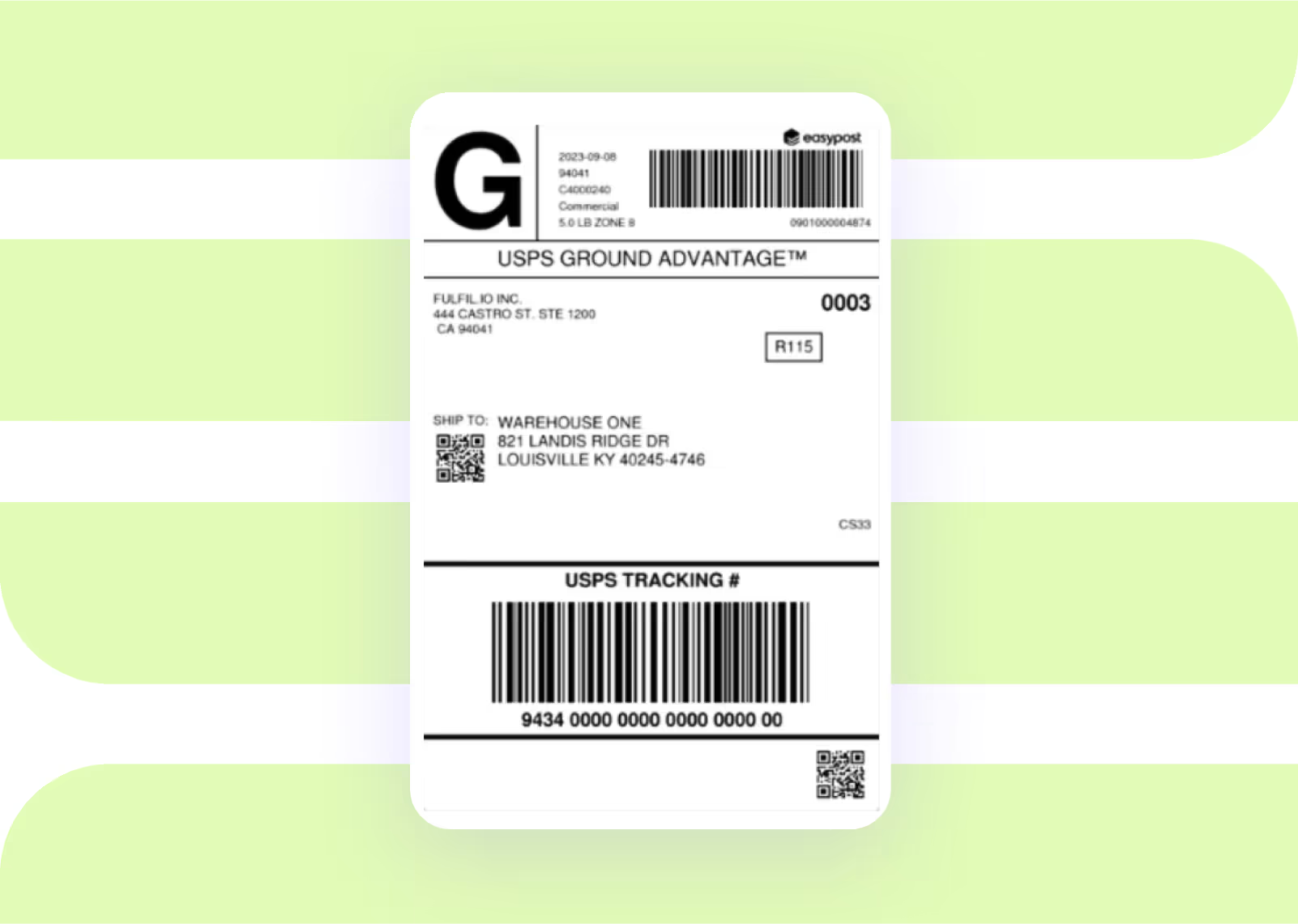
Intelligent shipping optimization
Automate label creation and rate shopping with built-in integrations to major carriers like UPS, FedEx, and USPS. Set up custom rules to automatically select optimal shipping methods based on order details, ensuring cost-effectiveness and timely delivery.
Flexible order management
Streamline operations with advanced features, including cross-docking support to move incoming products directly to outbound shipments, easy merging of multiple shipments, and the ability to split out unavailable items. Adapt quickly to inventory challenges and optimize fulfillment efficiency.
Seamless returns processing
Simplify the entire returns lifecycle with easy-to-use RMA creation and processing. Manage returns efficiently to enhance customer satisfaction and minimize operational disruptions.
CLIENT VOICE
Our results are proven, and our customers' experiences tell the story.
Everything you need for warehouse management
Mobile warehouse operations
- Mobile app for picking/packing
- Barcode scanning
- Real-time task management
- Optimized pick paths
Inventory management
- Real-time multi-channel tracking
- Multi-location inventory sync
- Cycle counting capabilities
- RFID and barcode integration
- Bin-level tracking
Key differentiators
- eCommerce-optimized
- Mobile-first approach
- Multi-channel capability
- Real-time visibility
- Flexible fulfillment options
Order fulfillment
- Cross-docking support
- Kitting and bundling
- Batch picking options
- Zone picking capabilities
- Multiple packing station management
Target market
- eCommerce businesses
- Multi-channel retailers
- B2B and B2C operations
- Companies needing flexible fulfillment options
Analytics & insights
- Performance metrics
- Staff productivity tracking
- Cartonization algorithms
- Real-time order status visibility
Shipping & returns
- Major carrier integrations (UPS, FedEx, USPS)
- Automated label creation
- Rate shopping
- Returns (RMA) processing
- Split/merge shipment handling
Main value propositions
- Reduced errors
- Faster fulfillment
- Better inventory accuracy
- Optimized shipping costs
- Improved operational efficiency
Frequently asked questions
How does Fulfil handle multi-location inventory management?
Fulfil provides real-time visibility across all your locations, allowing you to manage inventory levels, transfer stock, and fulfill orders from the optimal location. This ensures efficient inventory utilization and faster order processing.
Can Fulfil integrate with my existing warehouse equipment?
Yes, Fulfil is designed to work with a wide range of warehouse equipment, including barcode scanners, mobile devices, and label printers. Our system supports easy barcode scanning for accurate picking, packing, and inventory management.
What kind of warehouse analytics does Fulfil provide?
Fulfil offers comprehensive warehouse analytics including, picking efficiency, inventory turnover, order accuracy rates, and shipping performance. These insights help you identify areas for improvement and make data-driven decisions to optimize your warehouse operations.
Get started easily with a personalized demo
Our team of experts will assess your needs and goals for a personalized demo tailored for your brand to get you started with confidence.
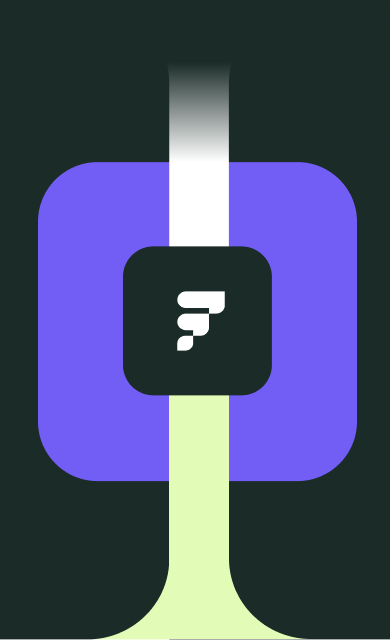
Thank you! Your submission has been received!
Oops! Something went wrong while submitting the form.