The (Last Minute) BFCM Ops Checklist
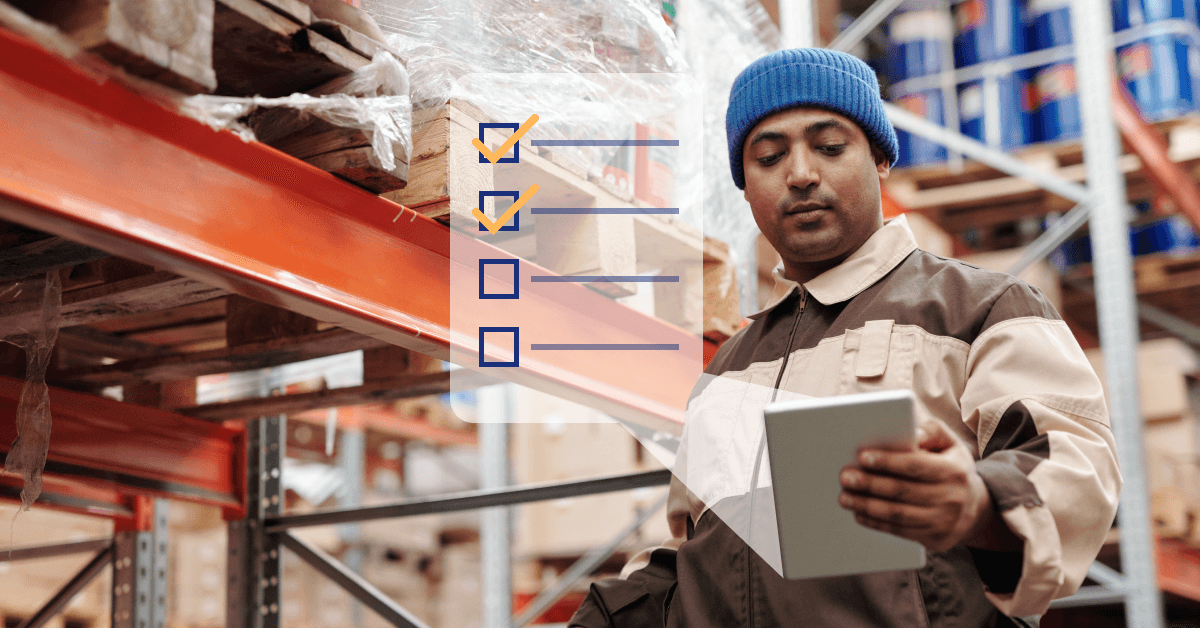
Introduction
With the Black Friday Cyber Monday (BFCM) weekend around the corner, here’s a last minute checklist for your operations team which can help make sure you’re set up for success this busy season.
🏷️ Switch to Pre-Generating Labels
To ensure that you get the most capacity out of each carrier, consider pre-generating shipping labels when possible. Carriers prioritize shipments chronologically from the time at which the label was generated, and pre-generating labels makes sure you stay at the top of the queue. Additionally, this will have the positive side effect of speeding up your packing stations, which will not need to wait for the label to generate. Learn more about carrier management for BFCM.
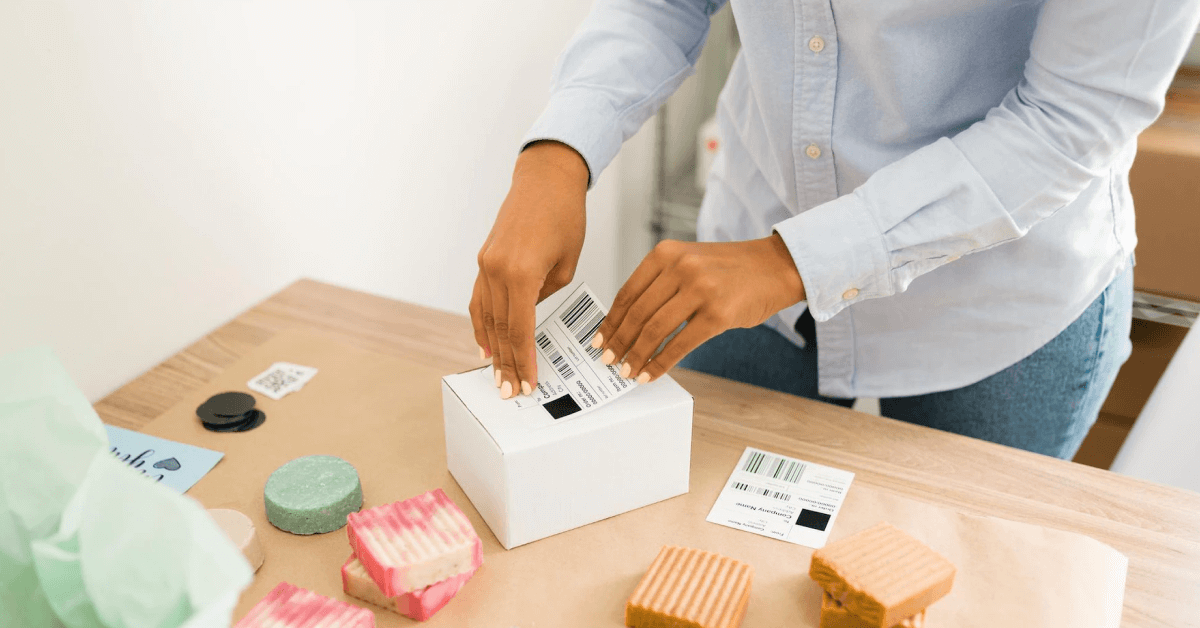
📣 Review Vendor Communication
Ensure that you have a reliable line of communication with your critical software vendors in case of emergency. Most vendors will have a Severity 1 (Business Critical) workflow that should be followed in these situations. Additionally, consider subscribing to the status pages of these vendors to be proactively notified of any service interruptions. Here’s a link to Fulfil’s status page.
🤖 Implement Automation
Any manual, human workflow that can be replaced by an automated, systemic process, should be. Doing this will minimize both the number of additional staff you’ll need, and the opportunity for human error. In particular, look for opportunities to automate Carrier and Service selection, package selection, replenishments, and printing. Here’s an article with more information about our recommended areas of automation.
📦 Review Batching Templates
Batching Customer Shipments is the process of grouping a series of orders together, and is the best way to make your pick, pack, and ship process more efficient. The batching process is typically governed by a series of Batching Rules that control which shipments should be grouped together. Having an effective Batching strategy is critical to keep goods flowing through your warehouse as smoothly as possible. To get you started, here’s a list of our top 4 recommended batching templates.
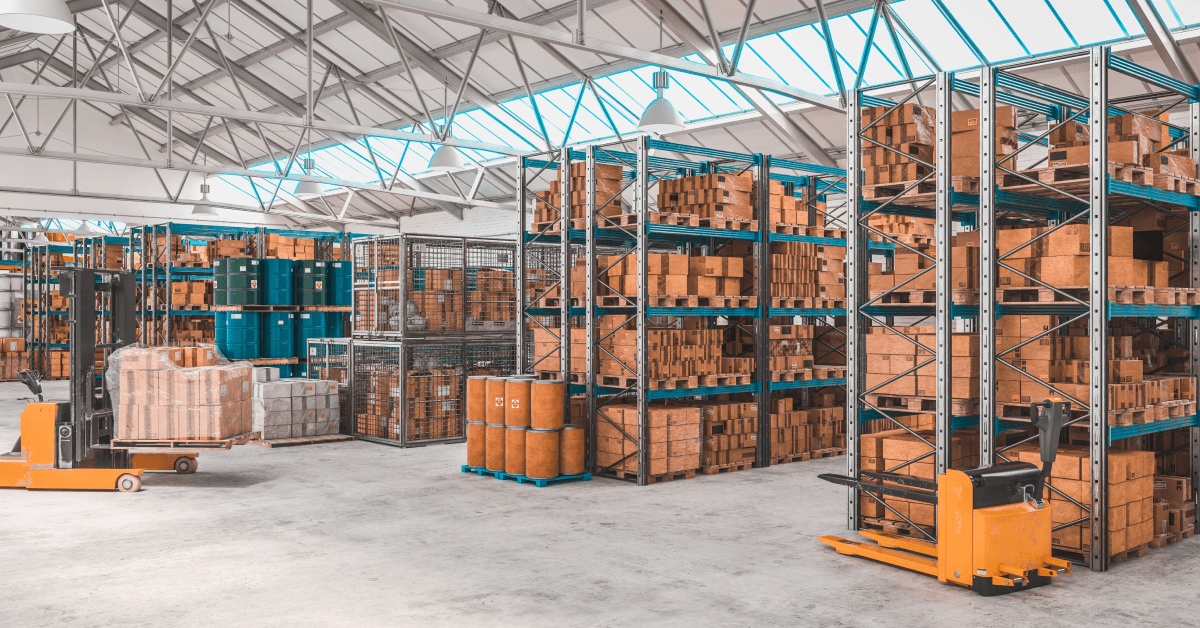
📜 Review Shipping Manifest Workflows
Make sure to regularly close shipping manifests throughout the day - don’t let manifests grow to over 500 shipments. Also, ensure that at the end of each day, all manifests are closed. This is because if a manifest is left open, the next day new shipments will begin entering the same manifest, which could cause an error when trying to close. As a general rule, ensure any label that is generated is on a closed manifest by the end of the same day.
🧊 Implement a Process Freeze
A Feature Freeze, or Configuration Freeze, is a point at which no further changes can be made to common workflows in your operations team. While there is always room for improvement, at a certain point the possible negative side effects of trying to implement a last- minute improvement can outweigh the potential benefits. Typically, we recommend implementing a process freeze at least 2 weeks before BFCM weekend.
📋 Ensure (easy) SOP Access
Standard Operating Procedures (SOPs) are critical to the success of onboarding temporary staff in your warehouse. They make the onboarding process smoother, and can help these new team members hit the ground running. However, regardless of how good the training process is, it’s always helpful to have a physical copy of the SOP for common workflows readily available for everyone in the warehouse. This is especially important for more potentially complex workflows like packing multi-item shipments. Here is our guide to creating SOPs for BFCM 2022, and check out the bottom of the article to download an SOP template.
{{cool-component}}
🚢 Diversify Carriers
It’s well known that carriers often run out of capacity during the Q4 BFCM and Holiday busy season, and without proper carrier diversification, these capacity limitations can be devastating to any operations team. To mitigate this risk, ensure that you can easily transfer shipments in bulk from one carrier to another, and that you are appropriately setting expectations with customers. For more information, check out our article dedicated to Carrier Management for BFCM.
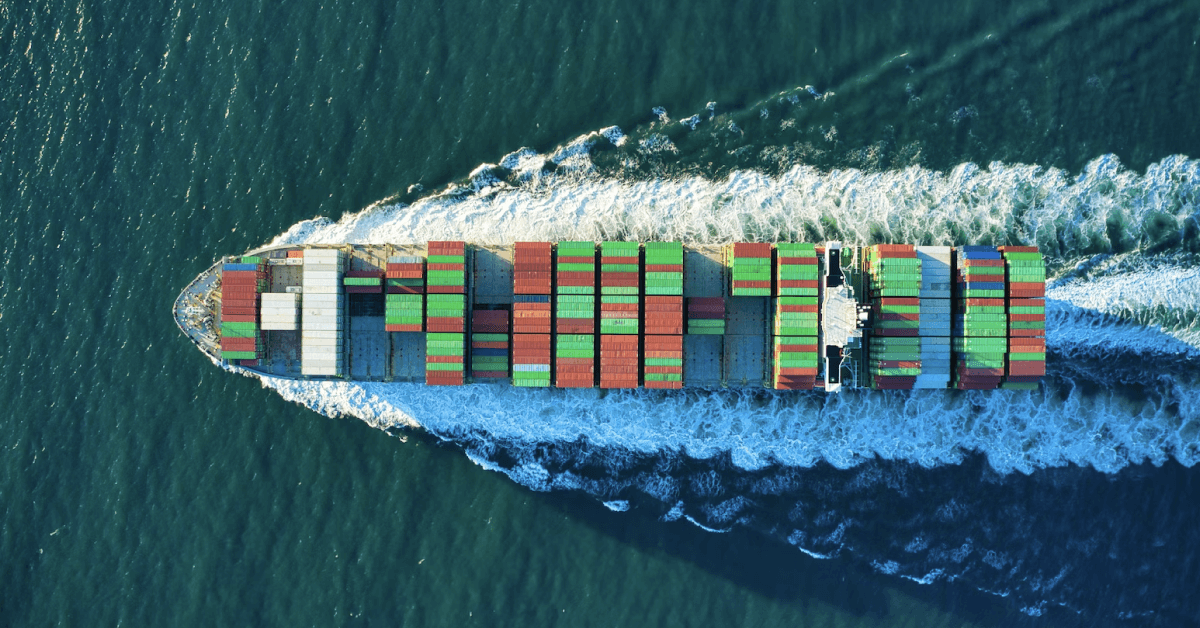
⚒️ Hardware Redundancy
Finally, double check to ensure that you have redundancies for critical pieces of hardware in your warehouse. Don’t wait for the label printer to break before buying a replacement, as this can cause significant downtime depending on the lead time of the item. In addition to printers, also consider having backup/spare picking equipment like mobile scanners, and packing equipment like mounted scanners.
Review
Anyone who’s been through a Q4 BFCM and Holiday busy season in the past knows that you can’t fully prepare for every possible hiccup that will arise. However, by carefully reviewing the above checklist and following these recommendations, you and your ops team will have the best shot at being ready for whatever is thrown your way! To see how Fulfil helps merchants like Mejuri and Ridge and many more crush their BFCM goals, book a demo with our team.
{{guide-form-component}}
Get Your Free Guide to Ecommerce ERP
More Reads on the Fulfil Blog
.png)
How Hoss Improved Their Amazon Seller Health with Fulfil’s Amazon Integration
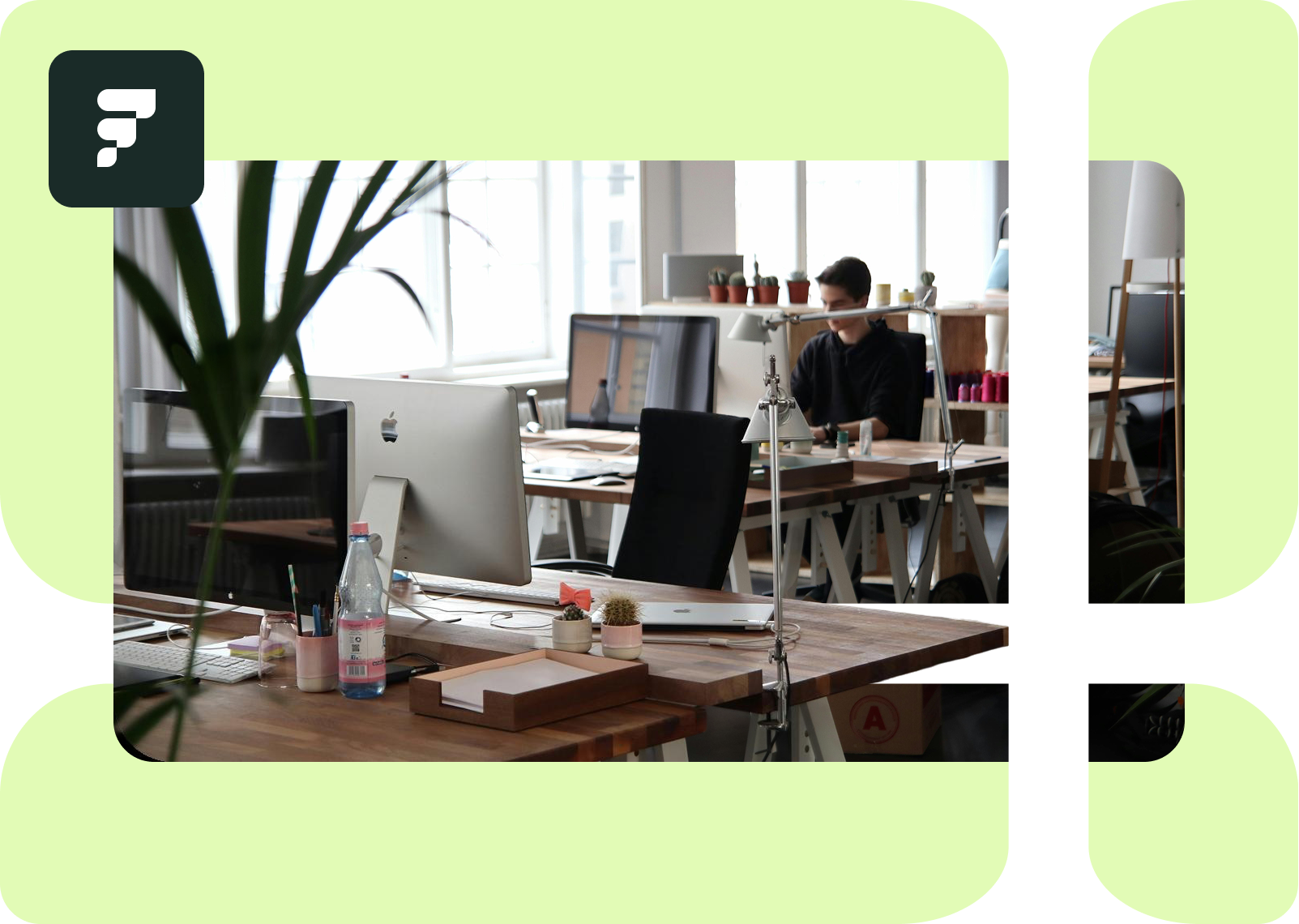
How Your Accounting Software Should Help Overcome Ecommerce Bookkeeping Challenges
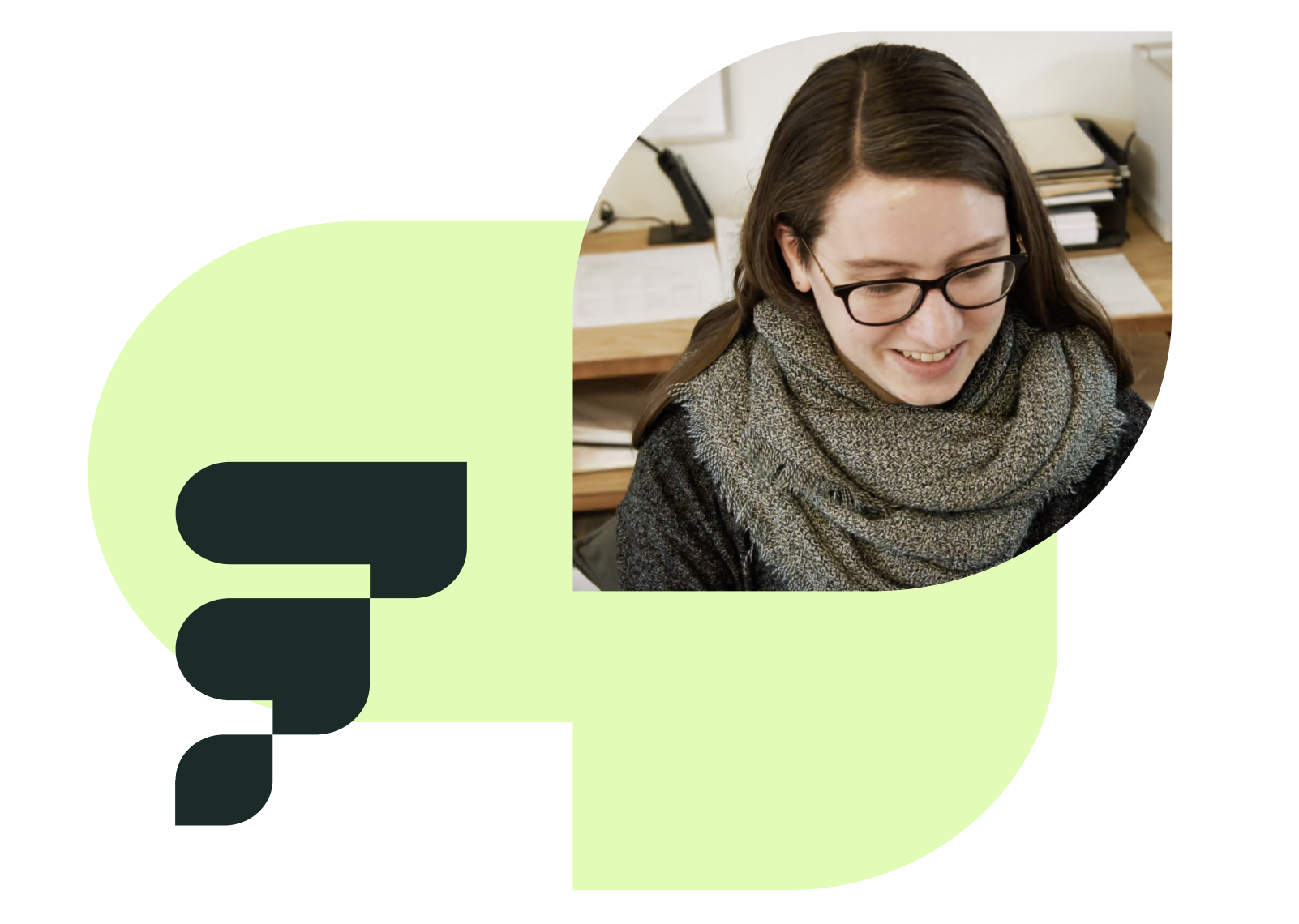
Revenue Recognition: Beyond the Basics
Get started easily with a personalized demo
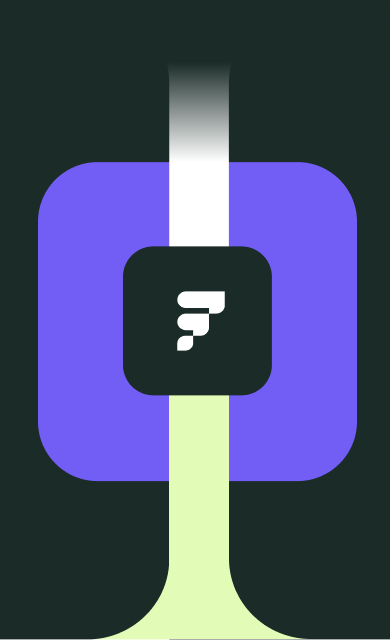