Creating SOPs for BFCM 2022
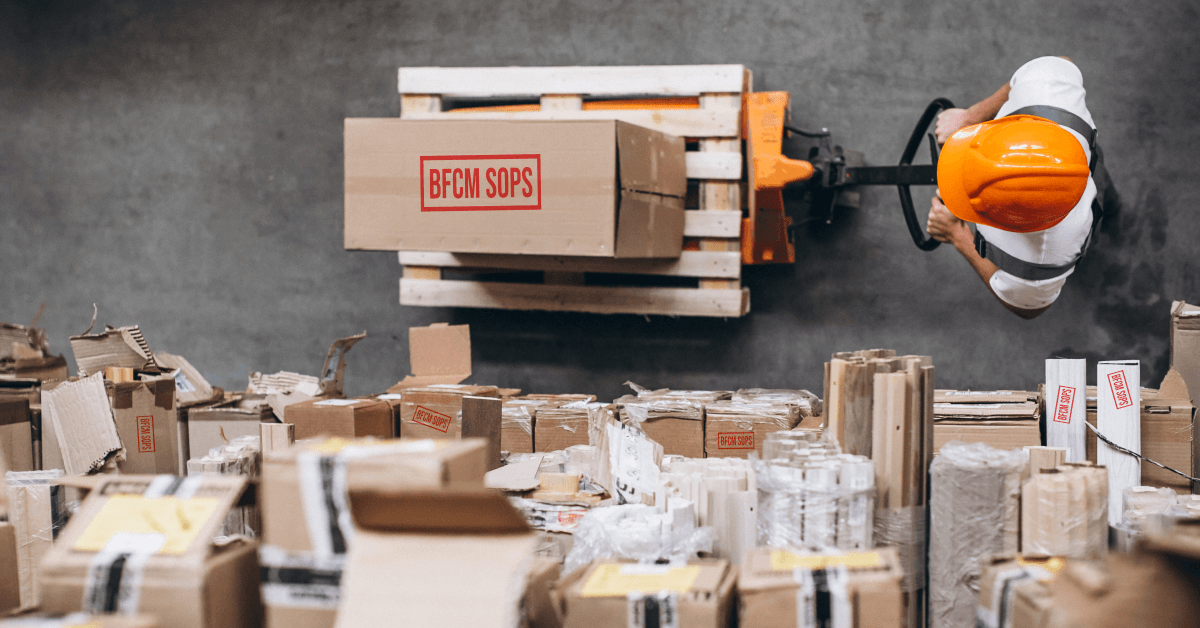
In order to support merchants through the BFCM chaos, we have developed some guidelines for designing and implementing SOPs for warehouse workflows for each function. Be sure to make a copy of our SOP template at the end of the article!
What are SOPs?
A Standard Operating Procedure (SOP) outlines the steps involved in a common process within a particular business area. Employees can refer back to the SOP to understand the intended workflow and outcome of a particular task.
Why do you need them?
By creating SOPs, you can dramatically speed up the process of onboarding new employees, as well as provide them with a reference guide and playbook to refer to later.
Simply by documenting today's process in detail, you can often find opportunities for improvement as a result of creating SOPs.
Your SOPs need not be archived at the end of BFCM either. Think of them as a living, breathing document that can evolve over time and serve as a place to iterate and improve every day. Operations aren’t written in stone, and need to be flexible, repeatable, and scalable far beyond BFCM.
What processes should you create SOPs for?
In most cases, SOPs are used for workflows with little variability, and in which several people perform the same task simultaneously. They are especially useful when it is important for the task to be carried out in the same way by multiple individuals.
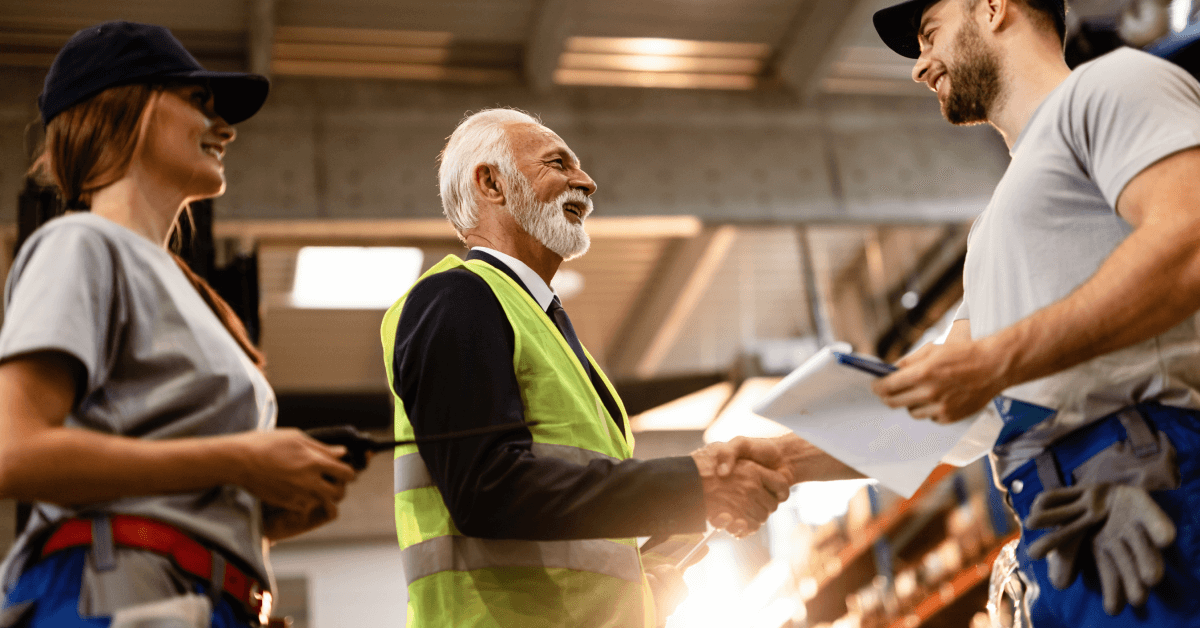
Within the Warehouse, consider creating SOPs for these areas:
Receiving
Product can’t be picked, packed, or shipped until it’s Received by the Inbound team. Carefully define SOPs for the following areas to keep product flowing smoothly:
- Customer Returns
- Supplier Shipments (Inspection)
- Transfers
Storage
Once product has been received and QC’d, it needs to be put into the bulk storage areas so that the pickable locations can be replenished. Consider:
- Supplier Shipments (Shelving/Put-away)
- Overstock
Inventory Control
All roads lead back to inventory control; the efficacy of the rest of the warehouse is dependent on the quality of the input data. Also make sure that the pickable locations are constantly stocked via an efficient replenishment system.
- Cycle Counts
- Bin Replenishment
Picking
Different order types require different workflows. Therefore, create separate SOPs for each unique type of order:
- Wholesale/EDI Orders
- D2C Orders
- Buy Online, Pickup in Store (BOPIS) Orders
- Internal Shipments (Store Transfers, Warehouse Transfers, etc)
Production
Production can be one of the most complex areas of a warehouse operation, which makes it especially important to carefully define SOPs. This will speed up the onboarding of new employees, and ensure consistency with the production output.
- Workstation Operation
- Runner (Replenish Materials, Inventory Management, etc)
Packing
Packing can easily become a bottleneck in larger warehouses, and is a common area to require seasonal help around BFCM. Create SOPs for Packing to speed up onboarding of new employees:
- Packing Workflow
- Runner (Replenish Packing Materials, Clearing Gaylords, etc)
{{cool-component}}
Shipping
All other areas funnel into Shipping - getting product out the door is critical to maintaining the throughput of the warehouse. Create separate SOPs for the different types of outbound shipments, to ensure one does not block the other.
- Shipping Workflow (Customer Shipments)
- Outbound Shipments (Store transfers, wholesale orders, etc)
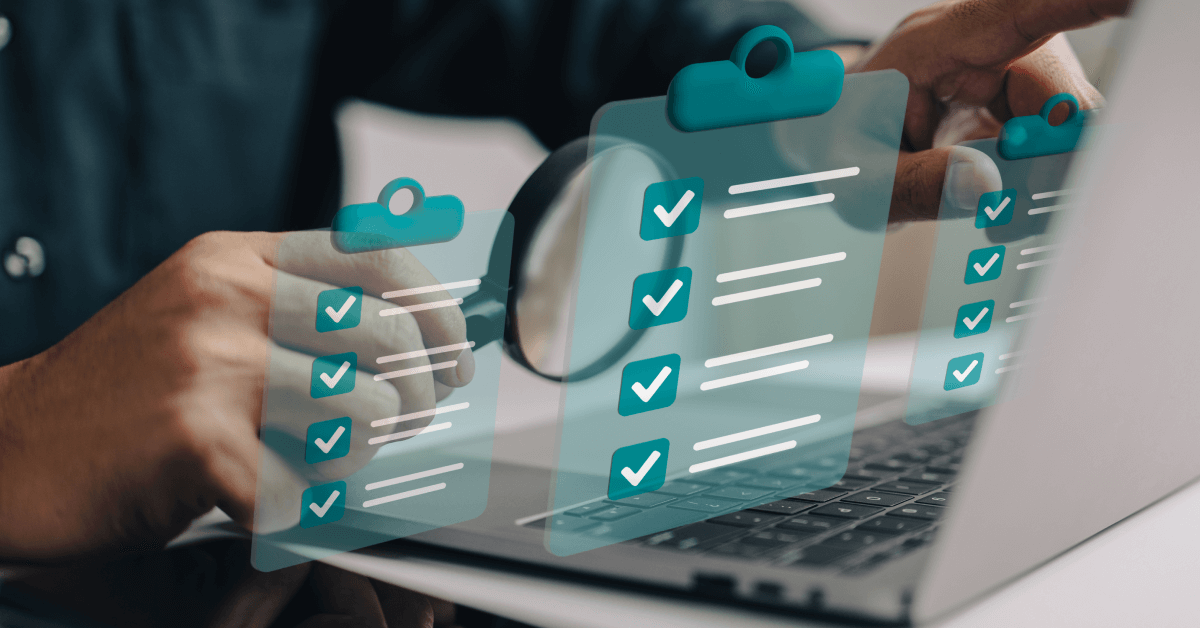
How should I create an SOP?
The following questions should be considered when creating an SOP:
1. What is the intended outcome of this task or workflow?
Starting from the end can help you create a clear and effective description of the specific steps your team will need to follow in order to accomplish this.
2. Which role is responsible for this workflow?
Knowing the audience, and catering the message towards them, is extremely important. Only include information that is directly relevant to the task at hand, which will help to keep the SOP concise. Additional context can be provided as needed, such as relevant workflows before or after the SOP, but shouldn’t be included in the SOP itself.
3. How long should this task take?
It’s important to include a benchmark of the expected time it takes to complete the task that the SOP is describing. This acts as a guide for new employees to understand if they are on the right track.
4. How often should this task be completed?
This can either be a specific time of day, or from a ‘trigger’. For example, a Bin Replenishment workflow only needs to be completed once a certain minimum inventory threshold has been hit. It’s good to know how to complete a task, but it’s equally important to know when to complete that task.
5. Where could there be confusion in the SOP?
Read through the SOP with a 3rd party who isn't familiar with the task, and look for areas where a new employee might get confused. If there are areas of confusion identified, askwhy- was it a lack of context? Or perhaps not enough detail in the step-by-step instructions? Was there missing information around where to go to complete a task? Use this feedback to remove ambiguity.
What’s Next?
Creating SOPs for common workflows in your warehouse will not only make it far easier to onboard new employees, but also inevitably uncover opportunities for improvement. These SOPs can be living documents for your team to improve upon, far beyond the BFCM period.
Click here to download our SOP Template to get started on your 2022 BFCM SOPs!
{{guide-form-component}}
Get Your Free Guide to Ecommerce ERP
More Reads on the Fulfil Blog
.png)
How Hoss Improved Their Amazon Seller Health with Fulfil’s Amazon Integration
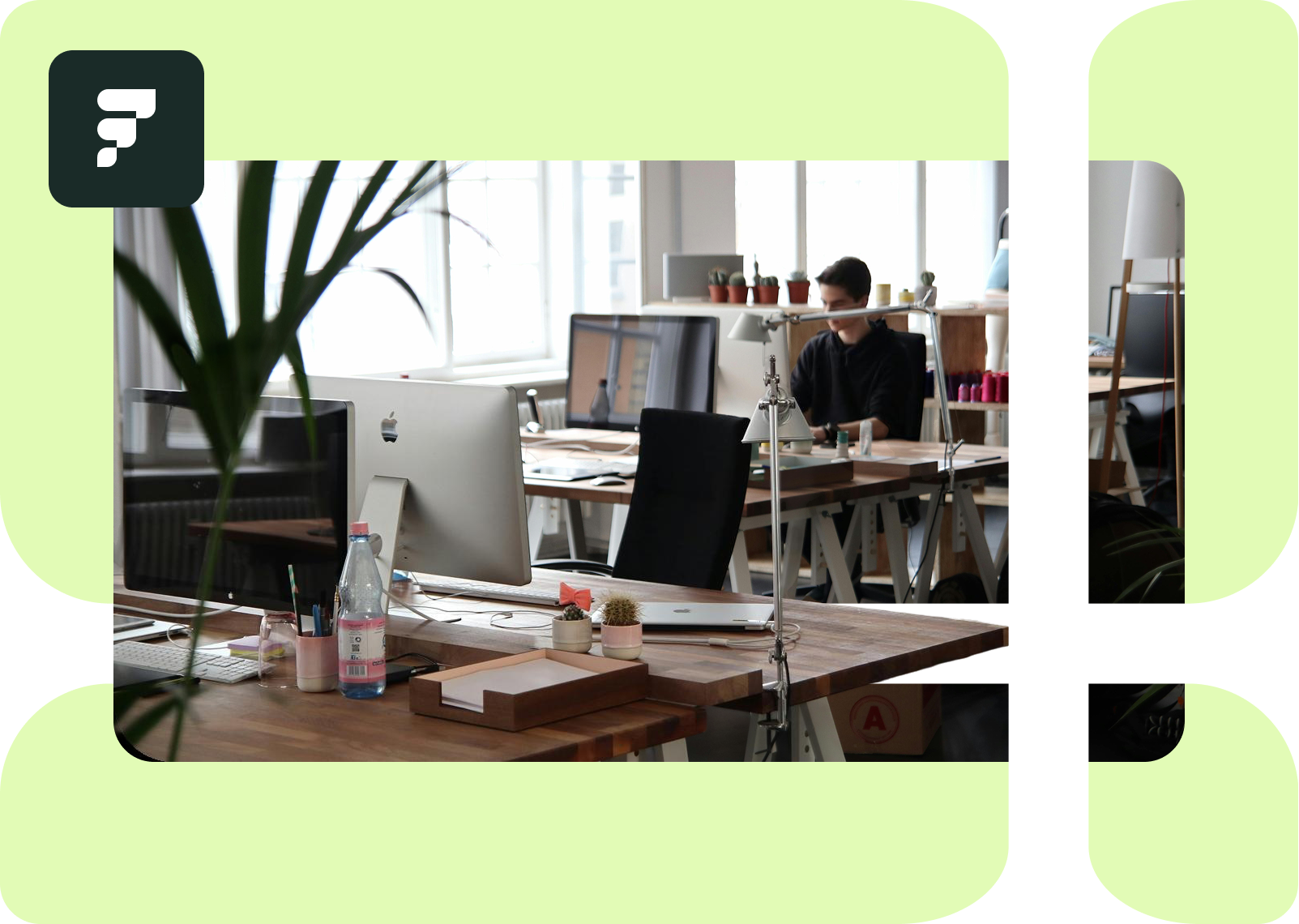
How Your Accounting Software Should Help Overcome Ecommerce Bookkeeping Challenges
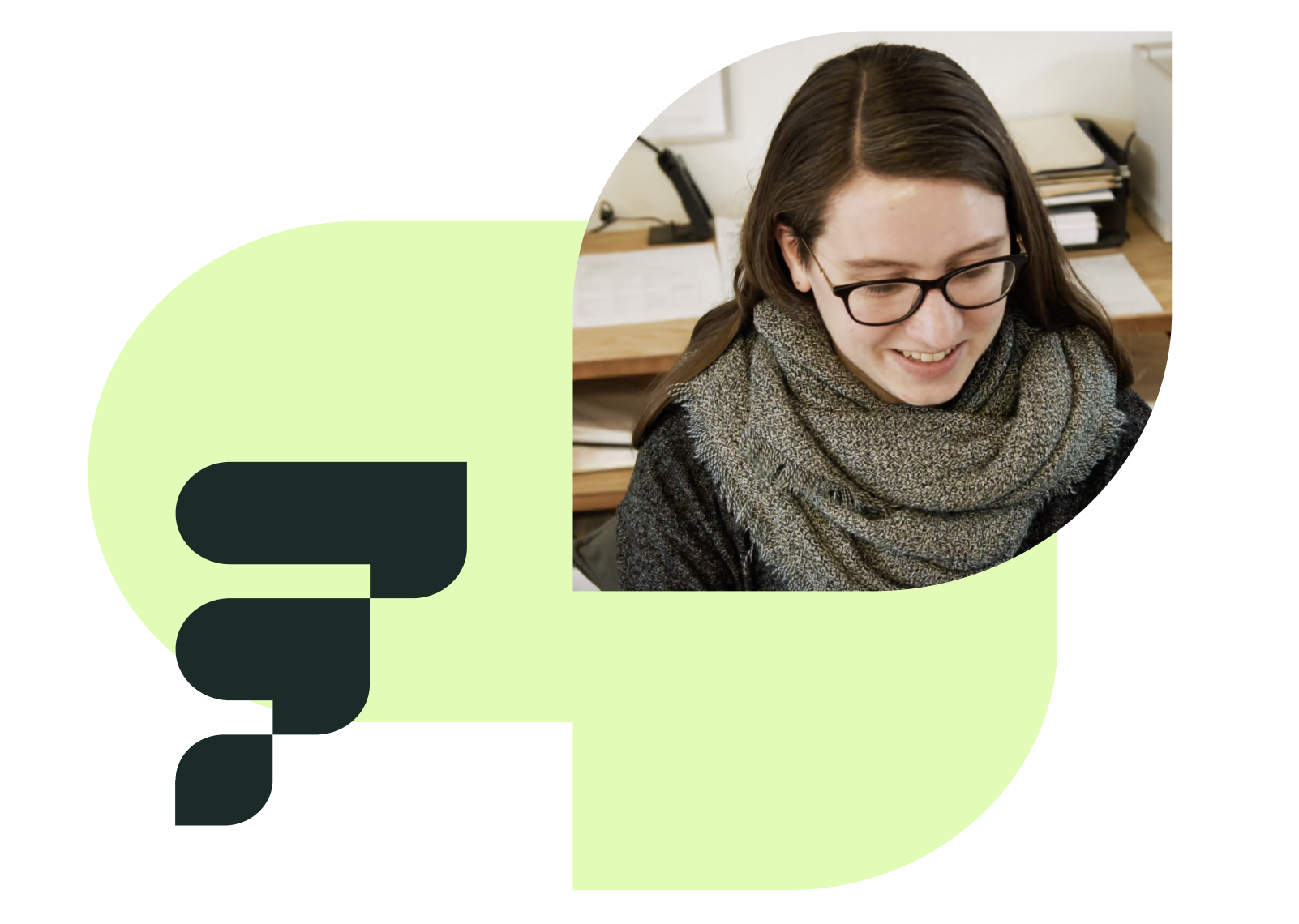
Revenue Recognition: Beyond the Basics
Get started easily with a personalized demo
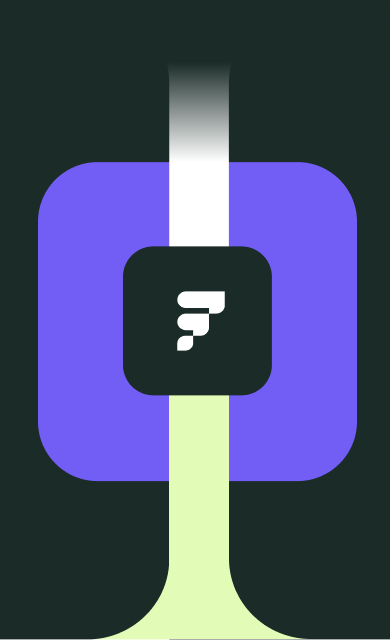