Lie-Nielsen's ERP Empowers their Team to Focus on their Craft
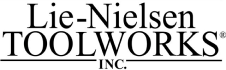
Overview
Lie-Nielsen is a manufacturer of working hand tools based in Warren, Maine. Founded 39 years ago by Thomas Lie-Nielsen, who followed his boat-builder father's footsteps into craftsmanship, the company has grown from producing a single tool to becoming a global distributor of fine woodworking tools. Today, the company employs 100 people and maintains worldwide distribution through both retail and wholesale channels.
Challenge
Six years ago, Lie-Nielsen faced the complex challenge of managing their growing business operations. They needed a comprehensive software solution that could handle multiple aspects of their business, including production management, inventory tracking, purchasing processes, production flow, sales order tracking, customer service, and shipping. As a manufacturer with both production and distribution needs, they required a system that could "wrap around all the needs of the business."
Solution
Lie-Nielsen implemented Fulfil as their comprehensive business management platform.
The system provides:
- Production management capabilities that enable orderly shop operations
- Inventory tracking functionality
- Purchase order management
- Sales order tracking
- Customer service support
- Shipping management tools
- Financial management features including journal entry generation
- Custom API integration for production order creation and bill of materials management
The company has also developed custom tools and reports within the system, including financial templates for faster journal entries and specialized production tracking capabilities.
{{demo-component}}
Results
The implementation of Fulfil has delivered significant improvements across multiple areas of the business. The shipping department efficiently manages picking, packing, and receiving operations through the platform, leveraging seamless carrier integrations such as Fulfil’s Shippo integration to drive efficiencies and optimize fulfillment costs. Custom reports provide management with a comprehensive view of operations, enabling them to track movement of parts and forecast inventory availability for customers.
The financial team has benefited from robust financial integrations such as Stripe and Authorize.Net, and streamlined processes, particularly in managing day-to-day operations such as cash and check deposits, expense tracking, and journal entry generation. The system has enabled better workflow tracking and data capture across all operations.
The production team has leveraged the API capabilities to automate various processes, including production order creation and bill of materials management. This automation has contributed to faster movement of parts through the shop and improved forecasting capabilities for customer orders.
What's Next
Lie-Nielsen continues to explore ways to leverage Fulfil's capabilities to enhance operational efficiency. The company's focus is on further automating processes to allow team members to concentrate on their core competencies. Their goal is to use the system to free up more time for strategic activities while maintaining the high quality of their traditional toolmaking craft. The platform's ability to support both manufacturing and distribution operations positions Lie-Nielsen well for continued growth and efficiency improvements.
Get Your Free Guide to Ecommerce ERP
Get started easily with a personalized demo
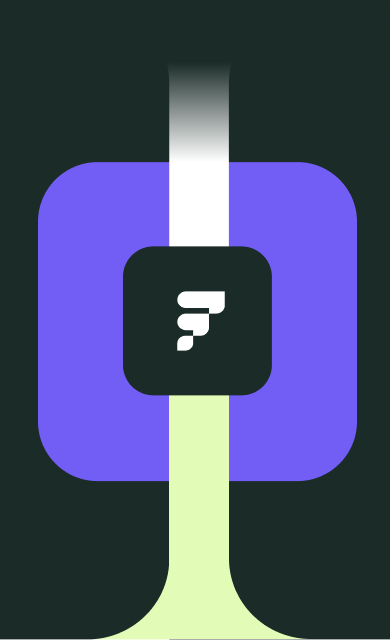