Inventory valuation methods: FIFO vs. Moving weighted average
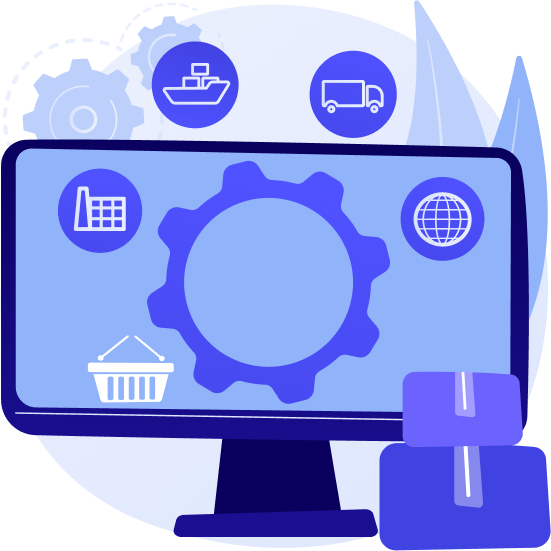
Inventory valuation methods play a crucial role in financial reporting and operational efficiency. Two prominent approaches, First-In, First-Out (FIFO) and Moving Weighted Average (MWA), merit close examination.
In this article, we explore the key differences between these methods and their implications for your brand.
FIFO: The traditional approach
FIFO assumes that the oldest inventory items are sold first. This method often aligns closely with the actual flow of goods in many businesses.
Under FIFO:
- New inventory shipments create additional cost layers.
- Cost of Goods Sold (COGS) is based on the oldest inventory layers.
- Returns and adjustments can be complex, potentially affecting multiple cost layers.
Moving weighted average: The Streamlined alternative
MWA recalculates the average cost of inventory with each new purchase.
The Moving Weighted Average offers several advantages
- All inventory items are valued at a single, current average cost.
- New shipments and returns are easily incorporated into the average cost.
- Inventory adjustments are straightforward, affecting only the quantity and not the cost layers.
Real-world implications
Inventory valuation methods significantly impact financial reporting and operational efficiency. Let’s explore different scenarios and their impact on cost accuracy, financial stability, and scalability.
1. Inbound Supplier Shipment
FIFO: The cost of received items is added as a new layer of inventory at the purchase price. When items are sold, the cost is based on the oldest layer.
MWA: The cost of received items is combined with the existing inventory, and a new weighted average cost is calculated. This new average cost is then applied to all inventory items. If there is no existing inventory, then the new average cost is the cost of the new shipment.
Example 1:
FIFO:
- Initial Inventory: 100 units @ $10 each
- New Shipment: 50 units @ $12 each
- Remaining Inventory Cost after sale of 100 units: 50 units @ $12 each
MWA:
- Initial Inventory: 100 units @ $10 each
- New Shipment: 50 units @ $12 each
- New Average Cost: (100 * $10 + 50 * $12) / 150 = $10.67 each
Example 2 (No Initial Inventory):
FIFO:
- Initial Inventory: 0 units
- New Shipment: 50 units @ $12 each
- Sale of 20 units: 20 units @ $12 each (all from the single layer)
- Remaining Inventory Cost after sale: 30 units @ $12 each
MWA:
- Initial Inventory: 0 units
- New Shipment: 50 units @ $12 each
- New Average Cost after Shipment: (50 * $12) / 50 = $12 each
- Sale of 20 units: 20 units @ $12 each
- Remaining Inventory Cost after sale: 30 units @ $12 each
2. Inventory Adjustment
FIFO: Adjustments (e.g., write-offs) impact the oldest inventory layer first. This can lead to complications if multiple layers exist.
MWA: Adjustments are straightforward, reducing the overall quantity and recalculating the average cost based on the remaining inventory.
Example:
FIFO:
• Adjustment: Write-off 20 units
• Inventory: Reduce quantity from the oldest layer, potentially leaving multiple cost layers.
MWA:
• Adjustment: Write-off 20 units at the current average cost ($10.67 from previous example)
• New Average Cost remains the same for the remaining inventory.
Example 2 (Inventory Adjustment - Units Found):
FIFO:
- Initial Inventory: 50 units @ $10 each
- Inventory Adjustment: Found 20 units (assumed to be at the oldest cost)
- Updated Inventory: 70 units @ $10 each
MWA:
- Initial Inventory: 50 units @ $10 each
- Inventory Adjustment: Found 20 units
- Updated Inventory:
- New Total Cost: (50 units * $10) + (20 units * $10) = $700
- New Total Units: 70 units
- New Average Cost: $700 / 70 units = $10 each
{{cool-component}}
3. Balance Sheet and Inventory Asset Account Value
FIFO: The inventory asset account value on the balance sheet is determined by taking the weighted average of the active cost layers.
MWA: The inventory asset account value is determined by calculating the average cost of all inventory items.
4. Customer shipments (Line Item Pulling from Two Costing Layers)
FIFO:
- Initial Inventory: 50 units @ $10 each
- New Shipment: 100 units @ $15 each
- Sale of 70 units:
- 50 units @ $10 each (from the oldest layer)
- 20 units @ $15 each (from the next layer)
- Remaining Inventory:
- 80 units @ $15 each
MWA:
- Initial Inventory: 50 units @ $10 each
- New Shipment: 100 units @ $15 each
- New Average Cost: (50 * $10 + 100 * $15) / 150 = $13.33 each
- Sale of 70 units: 70 units @ $13.33 each
- Remaining Inventory: 80 units @ $13.33 each
Performance Impact:
FIFO: Managing inventory with FIFO involves using multiple cost layers, which creates significant performance challenges. When processing orders, it’s crucial to ensure that two orders do not pull from the same inventory layer at the same time.
To prevent this, the system must lock each layer during the order processing, ensuring that no other order can access that layer until the first one is complete. This process, known as serial processing, means that orders are handled one at a time, which slows down the system and prevents it from processing multiple orders simultaneously (parallel processing).
This requirement for serial processing increases the complexity and overhead, making it harder to scale as the volume of orders grows.
MWA: With MWA, all inventory items are valued at a single average cost, eliminating the need for multiple cost layers. This simplifies the database operations as there is no need to lock specific layers during order processing.
Consequently, the system can process multiple orders simultaneously (parallel processing) without the risk of conflicts or errors, leading to faster performance and easier scalability.
Performance considerations
The choice between FIFO and MWA can significantly impact operational efficiency:
FIFO requires serial processing of orders to prevent conflicts between cost layers. This can significantly slow down order processing and limit scalability.
MWA, with its single average cost, allows for parallel processing of orders. This translates to faster performance and easier scaling - a crucial factor for growing businesses.
{{guide-form-component}}
The Bottom Line
While FIFO has long been considered the most theoretically correct method, MWA offers great advantages:
- It reflects the most recent cost of goods, enhancing financial statement accuracy.
- It smooths out cost fluctuations, leading to more stable financial outcomes.
- It simplifies inventory management and accounting processes.
- It allows for better scaling, particularly for businesses processing high volumes of orders.
The choice between FIFO and MWA depends on various factors including the nature of the business, its operational scale, and specific accounting needs. While FIFO might still be the right choice in some cases, the operational and scaling benefits of MWA are becoming increasingly relevant in today's fast-paced business environment.
Get Your Free Guide to Ecommerce ERP
More Reads on the Fulfil Blog
.png)
How Hoss Improved Their Amazon Seller Health with Fulfil’s Amazon Integration
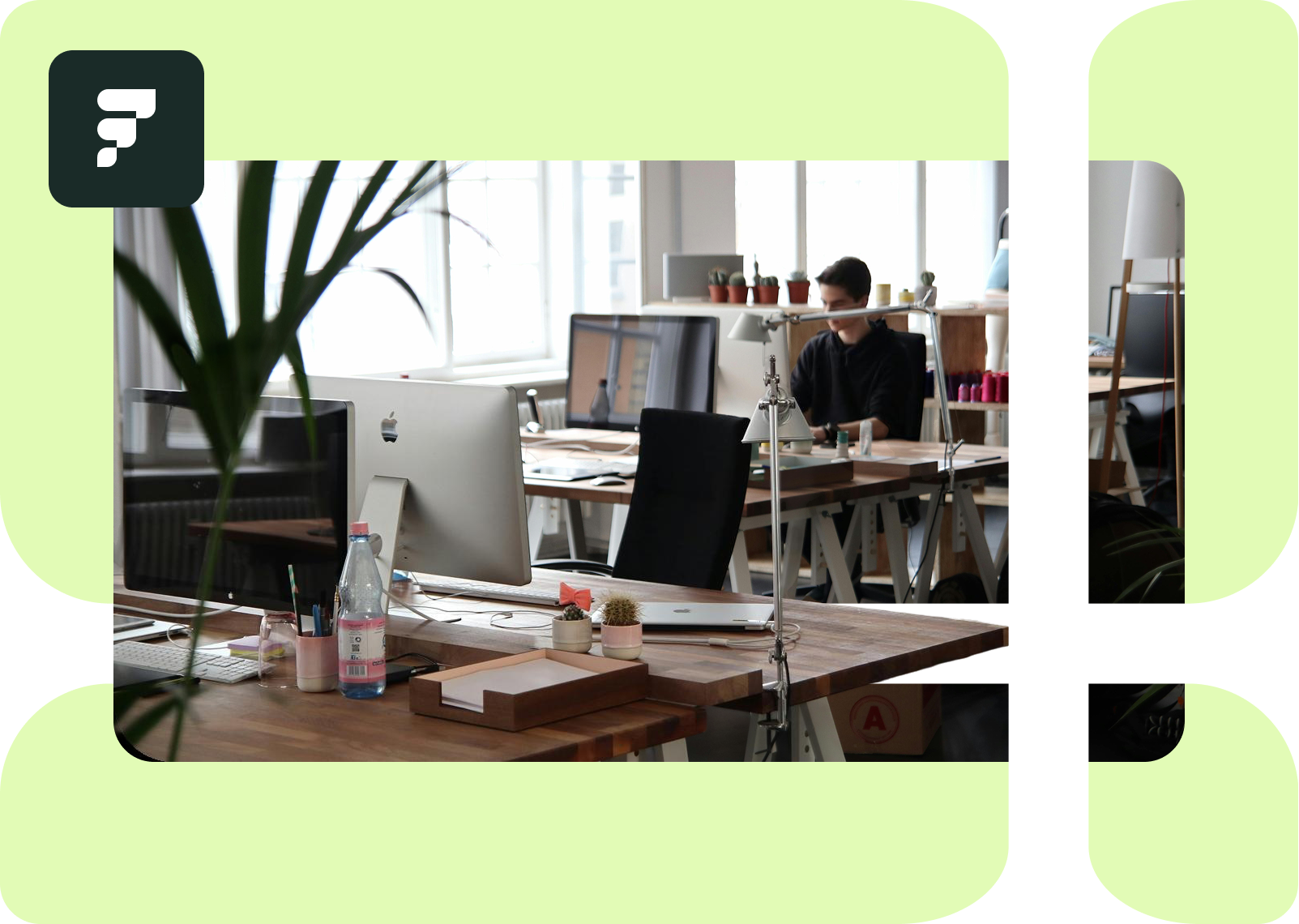
How Your Accounting Software Should Help Overcome Ecommerce Bookkeeping Challenges
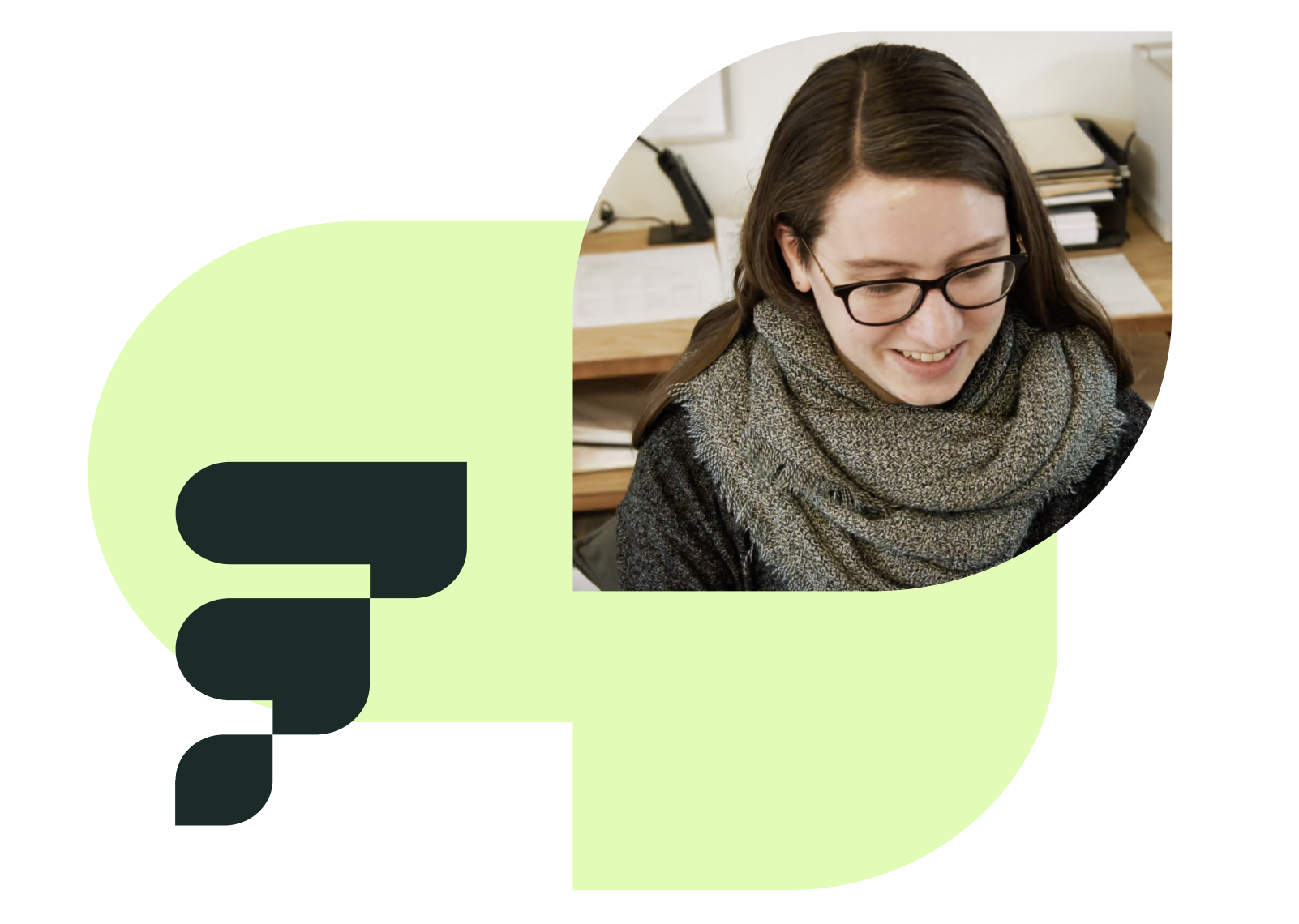
Revenue Recognition: Beyond the Basics
Get started easily with a personalized demo
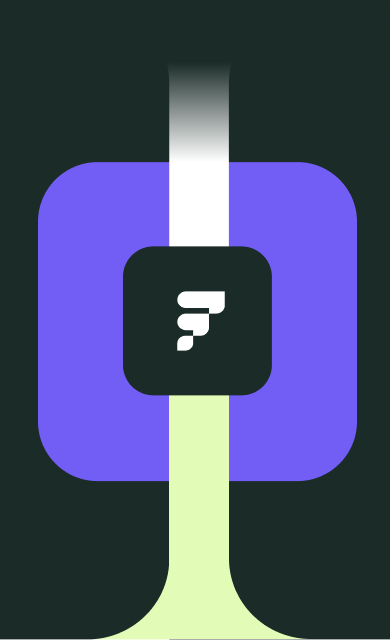